While the significant cost reductions seen across the solar industry in the last decade-plus have allowed the resource to expand exponentially in a relatively short period of time, this same growth has led to an issue that is only set to grow as each new project is built: flat, even land, the kind most optimal for development, won’t be available forever.
When developers need flat land that they just don’t have, they have historically turned to land grading, the effective and established process of excavating the dirt around a project site and moving it to create an area of even, level terrain.
This issue has only been exacerbated by the high adoption rates of single-axis trackers, which can promise solar project yield gains up to 35% more than conventional systems, when paired with other breakthrough technologies, like bifacial panels. These trackers, however, require the rows of panels mounted upon them to be at the exact same height and angle, requiring significant earthwork and longer foundation pile lengths, all of which add to project costs.
Developers faced with an uneven project terrain profile can encounter land grading cost estimates of more than 5% of total project budget, and that’s before the considerations of wind-blown dust, rainwater erosion, and any other relevant environmental variables are taken into account, which can all further drive up costs.
Hearing the concerns of site terrain and project land grading come up time and time again in conversations with customers, Nextracker decided to tackle the issues of sloping and undulating terrain head-on. The company has created the NX Horizon-XTR, a terrain-following, single-axis tracker built specifically for projects located on sites with sloped, uneven, and challenging terrain.
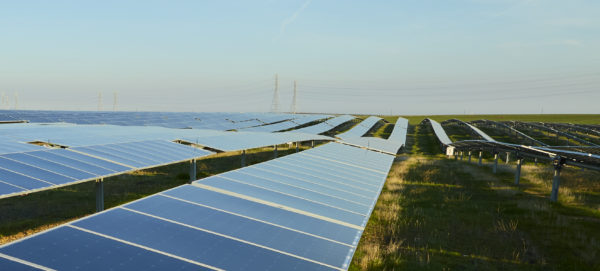
Image: Nextracker
“It’s often the case where we have customers that identify needs,” Nextracker CEO and Founder, Dan Shugar, told pv magazine in an exclusive interview. “So we had a customer about three and a half years ago, Swinerton (now SOLV), and they said, ‘Hey, your tracker is much more adaptive to terrain than you’re allowing in the specification, and we think there can be a lot of value there.'”
From that initial observation, the Nextracker team went to the lab to turn an ancillary strength into the main selling point for what the company hopes will be a market-shaping product. The breakthrough was initially enabled by Nextracker’s self-contained tracker motor, which allows each tracker row in an installation to operate independently from all of the other rows, referred to as adaptive tracking.
“[Adaptive tracking] allowed a whole range of benefits: we could self power the tracker with a little solar panel, instead of hooking up to the grid, and each row could be independent, meaning you could drive through the system for vegetation management, cleaning, maintenance on solar panels, or during construction,” shared Shugar “So if you’re on an if you’re on a hilly site, in the morning and sun’s on the east side, all of your trackers can all be at the ideal angle.”
Before adaptive tracking, tracker controls were largely on the project-level, meaning that if the angle for one row was adjusted, the angles of all modules across the project were adjusted.
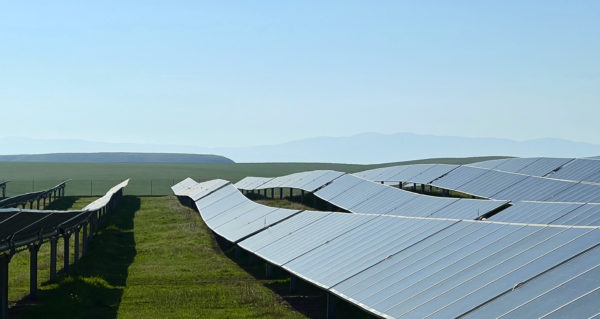
Image: Nextracker
When tracker controls are made more modular in nature, it allows for inter-row tweaks in layout and design, since the modules in that row can now be programmed to track at different angles over a different time period than even the other, adjacent rows.
To test the capabilities and new design requirements of the XTR, Nextracker reached out to SOLV, as well as a handful of other longtime partners, to pilot test the new product and provide notes to improve it.
“We did multiple pilot projects, we did a tremendous amount of engineering and reliability studies and monitoring,” Shugar explained. “And we launched this product called XTR: Extreme Terrain following. Essentially, what it allows you to do is to radically reduce the amount of earthwork you know, bulldozers, civil engineering, civil activity that happens on most sites, which radically reduces cost.”
“Once the engineering was validated and the tests were done, we supplied [XTR to] several dozen projects that are either completed or are under construction. We gave a few years of exclusivity on this, and then we’ve rolled it out to the rest of the industry, and we’ve had a tremendous amount of uptake.”
The result is a complete overhaul of traditional tracker design. Historically, all trackers in a row have been set to a standard plane, with the piers supporting the tracker and module units being installed at different lengths and depths to achieve that plane while maintaining structural and operational stability.
With XTR, the level plane philosophy has been discarded, and the design allows tracker rows to contour exactly to each row’s differing ground slope undulations.

The new usage cases unlocked by trackers that do not require a certain low-level land gradient are yet to be fully realized, but full of potential.
A 2021 study by Dr. Matthias Fripp, associate professor of electrical engineering at the University of Hawaii at Manoa, found that unlocking slopes of up to 20% gradient would make achieving the island’s renewable energy goals (100% by 2045) with solar the lowest-cost solution, while also keeping intact the majority of the island’s valuable agricultural land, a common point of contention between solar developers and the communities that house their projects.
Since those initial partner pilots, XTR has been constructed on over 3GW of cumulative projects, with more projects under construction or in late-stage development around the world. Existing installations utilizing the technology include SOLV’s Tygate 1 and 2 projects in Texas, which are 343MW and 258MW, respectively; SOLV’s Prospero 1 and 2 projects in Texas, which are 379MW and 326MW, respectively; and SOLV’s 68MW Broad River project, located in North Carolina.
By conforming to the existing ups and downs of north-south ground slope undulations, XTR sites have seen 30-90% less “cut and fill” earthmoving work, considerably reducing operating expenses and capital expenditures.
Less groundwork also means less disruption of the natural site where a project is located, a critical aspect for those, like Shugar, who believe that a solar installation should exist as harmoniously as possible with its surrounding environment.
“It accelerates the project, reduces risk, and saves in the operations and maintenance phase, because there’s less receding and vegetation management issues,” Shugar said. “Speaking, as an environmentalist, the topsoil is very fragile. A lot of the value of the topsoil is just in the upper strata of a few inches, you really don’t want to disturb that. And this technology allows that.”
This content is protected by copyright and may not be reused. If you want to cooperate with us and would like to reuse some of our content, please contact: editors@pv-magazine.com.
By submitting this form you agree to pv magazine using your data for the purposes of publishing your comment.
Your personal data will only be disclosed or otherwise transmitted to third parties for the purposes of spam filtering or if this is necessary for technical maintenance of the website. Any other transfer to third parties will not take place unless this is justified on the basis of applicable data protection regulations or if pv magazine is legally obliged to do so.
You may revoke this consent at any time with effect for the future, in which case your personal data will be deleted immediately. Otherwise, your data will be deleted if pv magazine has processed your request or the purpose of data storage is fulfilled.
Further information on data privacy can be found in our Data Protection Policy.