Sila Nanotechnologies, a battery materials provider, announced the commercial availability of Titan Silicon, a drop-in battery material that promises to increase electric vehicle range by 20%.
Titan Silicon replaces conventional graphite anodes with a nano-composite silicon anode that boosts performance and addresses supply chain issues related to graphite. The company announced plans to manufacture enough material to power one million EVs over the next five years.
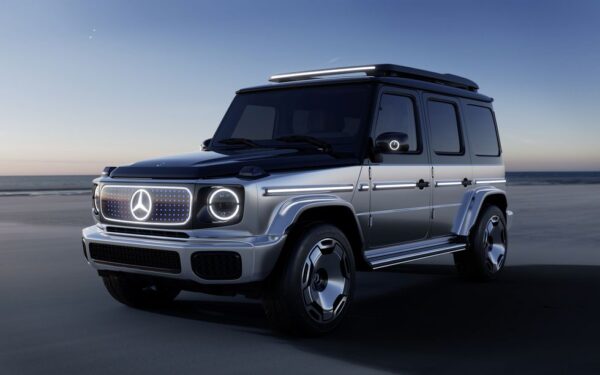
Image: Mercedes-Benz
In May 2022, Mercedes-Benz announced that it had selected Sila’s material for its luxury electric fleet, starting with the G-Class EV model, due out by mid-decade.
As graphite anodes and simple silicon compounds for lithium-ion batteries near their theoretical limits, new anode materials like Sila’s product are sought to extend range, meeting consumer expectations. The 20% range boost provided by the anode could result in up to 100 extra miles for some EVs.
Sila said its product can also dramatically improve battery charging time, charging a battery from 10% to 80% in just 20 minutes, even if the vehicle’s charge time is currently as long as 60 minutes. The company said it targets reducing the 10% to 80% charge time to approximately 10 minutes in the future. These gains in fast-charge time come without sacrifices to cycle life or safety while maintaining low swell, said the company.
The advanced anode material benefits from up to a 15% reduction in battery weight and 20% increase in space compared to conventional lithium-ion batteries, the company said.
The material is currently used in mobile fitness trackers. Titan Silicon is a “drop-in” solution, compatible with any cell form factor, including cylindrical, pouch and prismatic cells.
Sila offers customers a choice of partial or complete graphite replacement based on automaker or cell manufacturing performance goals. Today, over 90% of graphite is mined or processed in China, posing potential supply chain challenges for a high-graphite product.
The materials are all U.S. made, helping contribute toward battery integrators and automakers achieving domestic sourcing goals to qualify for Inflation Reduction Act incentives. The company said its silicon generates 50% to 75% less CO2 per kWh than graphite during production. Sila is also ISO 9001:2015 certified.
A survey conducted by the company found that nearly 90% of respondents who own or intend to purchase an EV view high-performance battery technology as more valuable than other tech enhancements or luxury features, including autonomous driving capabilities.
“Titan Silicon is the highest performing nano-composite silicon in the market today. Our battery and materials teams are constantly iterating and improving upon our chemistry to deliver the best, and most cost-efficient results possible,” said Gene Berdichevsky, co-founder and CEO of Sila. “With the wide adoption of EVs, consumers are looking for best-in-class solutions that deliver best-in-class performance, and our solutions provide just that: longer range and faster charge.”
The material has been developed for mass production, with a facility expected to come online in the second half of 2024 at the company’s Moses Lake, Wash. site.
This content is protected by copyright and may not be reused. If you want to cooperate with us and would like to reuse some of our content, please contact: editors@pv-magazine.com.
By submitting this form you agree to pv magazine using your data for the purposes of publishing your comment.
Your personal data will only be disclosed or otherwise transmitted to third parties for the purposes of spam filtering or if this is necessary for technical maintenance of the website. Any other transfer to third parties will not take place unless this is justified on the basis of applicable data protection regulations or if pv magazine is legally obliged to do so.
You may revoke this consent at any time with effect for the future, in which case your personal data will be deleted immediately. Otherwise, your data will be deleted if pv magazine has processed your request or the purpose of data storage is fulfilled.
Further information on data privacy can be found in our Data Protection Policy.