Concentrated solar power (CSP) uses mirrors called heliostats to direct sunlight into a collection tower, storing heat energy in abundant mediums like rocks, sand, or molten salt for highly available energy dispatch. High-heat and available energy is a key element in many machine and industrial processes, so the National Renewable Energy Laboratory (NREL) and the Department of Energy (DOE) are working on the next generation of CSP facilities.
The Gen3 CSP program targets an energy cost of 5 cents per kWh. DOE has identified opportunities in three material pathways: storing heat in sand-like particles, in liquids like molten salt, and in gases, such as the technology developed by Brayton Energy. DOE selected particle-based storage as the main method for its funding, but also opened the door for NREL to run a two-year liquid molten salt research program.
Challenges and breakthroughs
NREL’s Craig Turchi, a leader in thermal energy science and technology, said molten salts are a desirable option for heat transfer and storage as they are easy to work with and can be pumped through pipes and heat exchangers. However, there are some practical challenges, which Turchi’s team is currently working on overcoming.
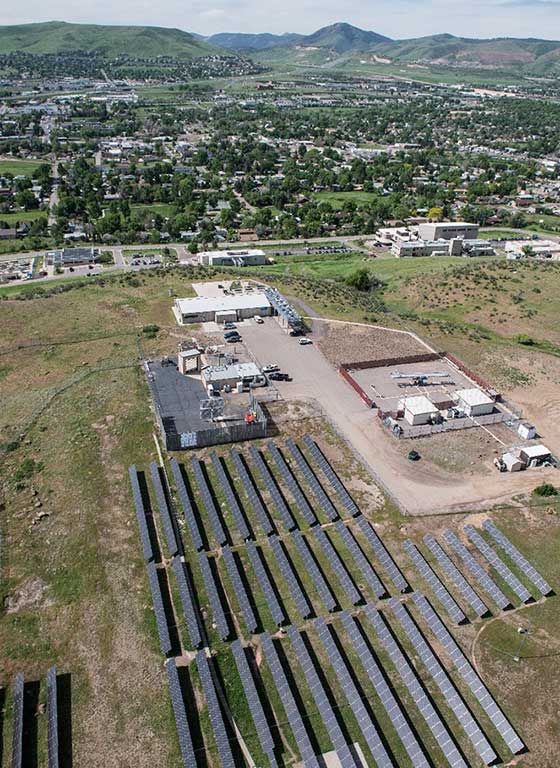
Image: Dennis Schroeder, NREL
Though molten salts are easy to move, they are also corrosive to their holding tanks and pipes. Turchi said, “We actually solved that problem by and large. NREL and partners did a lot of great science on the salt chemistry—how to purify it, how to make it relatively noncorrosive if you control the chemistry, and we demonstrated that in the lab.”
The next hurdle was finding the right kinds of salts for the Gen3 CSP liquid path. Commercial systems often use nitrate salts, but NREL said these begin to degrade at higher temperatures. NREL targets high temperatures for more efficient energy conversion, so it settled on chloride salts for their higher level of stability under extreme temperatures.
Another challenge is keeping the storage tank hot. The molten salts used freeze at 400°C, so extra insulation is needed. Turchi added, “Our design is a steel tank, but whereas the current tanks are insulated on the outside, our proposed tank was insulated on the inside to protect the steel.” DOE awarded NREL $2 million to build a prototype tank, which is being built on NREL’s Golden, Colorado campus.
Kerry Rippy, an NREL expert in inorganic chemistry, and her team explored electrochemical methods to further remove corrosive impurities in molten chloride salt. She is also developing electrochemical sensors to be placed inside storage tanks to monitor the purity of the salts during experimentation.
“There are multiple potential avenues for this research to be valuable. It can be beneficial for solar fuel synthesis; it could enable high-temperature fuel cells, and the nuclear industry is also really interested in this research,” said Rippy.
“The nuclear industry is developing a number of ‘Gen4’ reactors of its own, some of which use molten chloride salts,” said Turchi.
Decarbonized industrial processes
Solar PV and energy storage are excellent in providing reliable electricity, but some industrial processes require high-heat or large amounts of available energy. This has led to developments in CSP, and in other technologies, which are already being met with commercial success.
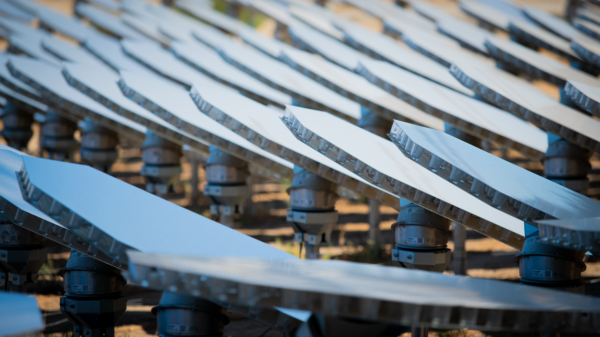
Image: Heliogen
Recently, startup company Rondo Energy closed a $22 million Series A funding round to scale its renewable energy heat batteries. The membrane-based battery stores solar and wind energy in solids at temperatures over 1200°C. The company said it plans to begin manufacturing and delivering systems to customers later this year.
In November, Heliogen partnered with Bloom Energy to create green hydrogen fuel. Heliogen’s CSP creates heat, steam, and electricity from concentrated sunlight. It was paired with Bloom’s solid-oxide, high-temperature electrolyzer to make the fuel. The company said hydrogen can be made 45% more efficiently than low-temperature PEM and alkaline electrolyzers. Electricity dictates nearly 80% of the cost of hydrogen from electrolysis. The CSP method reduces the need for electricity, using heat to aid its operations.
This content is protected by copyright and may not be reused. If you want to cooperate with us and would like to reuse some of our content, please contact: editors@pv-magazine.com.
By submitting this form you agree to pv magazine using your data for the purposes of publishing your comment.
Your personal data will only be disclosed or otherwise transmitted to third parties for the purposes of spam filtering or if this is necessary for technical maintenance of the website. Any other transfer to third parties will not take place unless this is justified on the basis of applicable data protection regulations or if pv magazine is legally obliged to do so.
You may revoke this consent at any time with effect for the future, in which case your personal data will be deleted immediately. Otherwise, your data will be deleted if pv magazine has processed your request or the purpose of data storage is fulfilled.
Further information on data privacy can be found in our Data Protection Policy.