Before COVID, global sales of new passenger cars were about 80 million units annually, growing slowly. During 2020, sales of internal combustion engine cars (ICEs) plunged, and sales of electrical vehicles (EVs) took off around the world. Today, EV sales are expected to grow exponentially for the rest of the decade, reaching 30 million and 60 million by 2040. This growth will generate more than 7 trillion dollars of EV sales before 2030, the fastest and largest shift in any global market in the last 100 years.
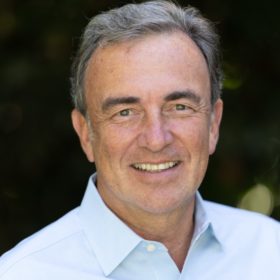
As desire for electric vehicles to deliver faster charging speeds, longer range and be more affordable increases, automakers are looking to find new and innovative solutions to satisfy this demand. However, creating a new market of vehicles — 100% of EV fleets for many automakers — is uncharted territory and to do so in a cost-effective manner takes time, scale, and new manufacturing systems.
The expected growth in EV sales during this decade will be dependent on an increase in the production of higher performance and lower cost EV batteries. Batteries are expensive, complex, and require specialized materials and chemicals. The EV supply chain requires huge increases in raw materials production and processing to feed into the huge increase in EV battery factories required to meet EV market demand.
The dynamics of EV cell production
EV cells are produced in large factories named “Giga-factories” because their production capacity is measured in GWh, where the letter “G” stands for billions of Wh of energy storage. In 2020, the global Gigafactory capacity was about 700 GWh and it is now expected to reach close to 5000 GWh by 2030.
When charging an EV, the electrons are stored almost exclusively in the graphite in the anode electrodes of the EV cells, where each electron is paired with a lithium ion until released during driving. Thus, EV-grade graphite annual production will need to increase from about 500,000 tons (500M Kg) to more than 3,500,000 tons (3.5 trillion Kg) by 2030. Today, a single 20 GWh factory requires a daily amount of graphite equal in weight to a Boeing 767.
The impact on the supply chain
Because batteries are heavy, they must be produced close to the EV factories and the sourcing and processing of specialized materials should ideally be on the same continent, from multiple suppliers carefully selected to avoid unnecessary costs and strategic shortages.
If this was not challenging enough for EV makers, they must also innovate at a rapid pace to incorporate new materials and new manufacturing processes so that EV batteries can provide longer range, charge faster, and cost less. A failure to do so will cost billions in lost revenue and market share will shift to competitors able to innovate faster, more safely and with greater economies of scale.
This represents the most daunting supply chain challenge ever faced by the incumbents in a large global industry: they must re-invent their own competencies and integrate new technologies from new suppliers to succeed.
The risks and the complexity of this challenge arise from the “perfect EV storm” — a trifecta of requirements that are difficult to address on their own, and exponentially so when combined.
- New Battery Technology: First, EV makers must secure and deploy new battery technologies to meet end-users’ demand for higher EV range, faster charging, lower cost, and lower carbon footprint. The rate of innovations to meet these requirements must be greater than in the last several decades.
- Secure Production of Raw and Processed Materials: Second, EV makers must also secure the production of raw and processed materials required to build EV batteries. The production and processing of these materials needs to grow at more than 30% compounded annual growth rates (CAGR) for the next ten years.
- Integrate into EV Cells: Third, EV makers must also ensure the integration of these materials into EV cells, at very high yield and without systemic safety failures. Because EV batteries are heavy, supply chains must be established in each of the major continents.
Looking ahead
The strategic question is how to reduce technical and financial risks while competing with other competitors in a race for market share in the global marketplace of hundreds of millions of EVs, worth trillions of USD in revenues.
The answer lies in a reevaluation of the supply chain in the following ways:
- It will be critical to secure access to innovations that are well protected by global patent families so that large investments can be made with the so-called “freedom to operate.”
- Material innovations must be analyzed in terms of access to large amounts of precursors and proven manufacturing equipment to reduce capex investment and scale-up risks.
- The manufacturing processes must be compatible with multiple material suppliers and multiple cell suppliers on each continent, to avoid single sourcing issues and enable strategic localization.
In order to be compatible with multiple material suppliers — we must think of a new process that replaces inefficient steps in the process by deploying salable technology that increases performance and decreases costs of the materials and cells used in EVs. Given that the end to the supply chain challenges we’ve been experiencing seem nowhere in sight, a positive future for EV battery manufacturing will be contingent on finding solutions that work within existing realities.
***
Vincent Pluvinage, PhD, is the CEO and co-founder of OneD Battery Sciences which has developed SINANODE, a set of technologies that “supercharge” the amount of energy stored, speed of charging, and power delivered to EV batteries. Vincent graduated summa cum laude from Université Catholique de Louvain in Belgium where he studied Applied Physics Engineering.
The views and opinions expressed in this article are the author’s own, and do not necessarily reflect those held by pv magazine.
This content is protected by copyright and may not be reused. If you want to cooperate with us and would like to reuse some of our content, please contact: editors@pv-magazine.com.
By submitting this form you agree to pv magazine using your data for the purposes of publishing your comment.
Your personal data will only be disclosed or otherwise transmitted to third parties for the purposes of spam filtering or if this is necessary for technical maintenance of the website. Any other transfer to third parties will not take place unless this is justified on the basis of applicable data protection regulations or if pv magazine is legally obliged to do so.
You may revoke this consent at any time with effect for the future, in which case your personal data will be deleted immediately. Otherwise, your data will be deleted if pv magazine has processed your request or the purpose of data storage is fulfilled.
Further information on data privacy can be found in our Data Protection Policy.