Much ink has been spilled over the lawsuit filed by Walmart against Tesla, related to the fires at solar installations on the roofs of its stores. But few journalists have asked why these fires happened in the first place, especially with technical literature stating clearly that properly installed solar arrays do not start fires.
And right there is the first clue – that the problems may not be in the arrays themselves, as much as how they were installed. A quick search for “connector” shows that this word appears dozens of times in the summons filed by Walmart on August 20, 2019.
Not only does Walmart allege that the fires at stores in Milpitas and Lakeside, California were started by faulty connectors, but the company also claims that Tesla staff had mated connectors that were incompatible with each other, that they had failed to torque the connectors adequately, and had failed to replace faulty connectors or to properly torque these following inspections, all of which resulted in unsafe conditions.
As revealed in a later report by Business Insider, Tesla had been running an internal program to replace these connectors, which were identified as Amphenol H4 connectors. Amphenol has denied that its connectors had anything to do with the fire, but this latest news is another black eye for the company following SolarWorld’s recall of modules using Amphenol connectors two and a half years ago.
However, pv magazine research indicates that the problems with connectors and their installation is much deeper than any one manufacturer or installer, and that issues with connectors could be a ticking time bomb for the solar industry.
“I would love to say it is a one-off situation, but it is a very prevalent issue in the industry,” notes Brian Mills, product manager – photovoltaics for Stäubli, which under the former name of Multi-Contact supplied connectors for nearly half of the solar online globally.
Compatibility?
Stäubli cites a Failure Modes and Effects Analysis (FMEA) by the EU-funded Solar Bankability Project, which identifies using different kinds of connectors – a practice known in the industry as “intermating” – as by far the leading cause of module failure, with various kinds of connector failures identified as the most costly problems.
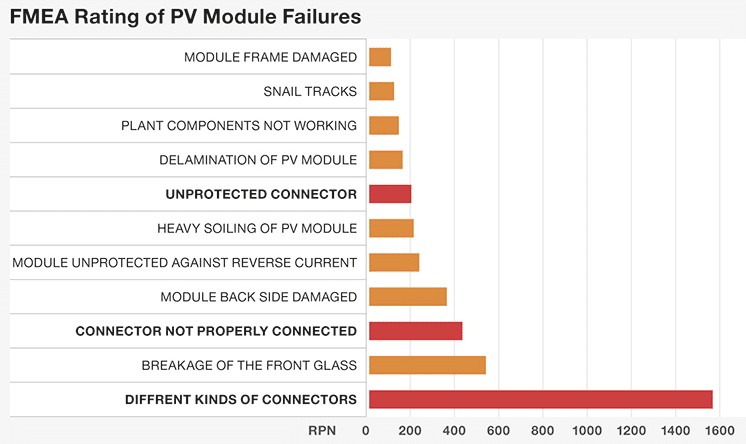
To be clear, this doesn’t mean that every connector issue ends in a blazing roof or field. But it does indicate that connectors have been a source of major problems.
To understand why this is such an issue, certain basic facts about connectors must be understood. Each connector manufacturer makes their product to their own internal standards, and while these products are typically certified by UL or other organizations, there is no single standard for connectors like there is for the electrical plugs that go into wall sockets.
And the differences are not superficial. Connectors are made of many different materials, and Shoals Technologies CEO Dean Solon notes that while many of the high-end connectors have copper contacts, some manufactures use bronze or aluminum alloys, and says that he has even seen steel contacts.
Additionally, there is no one standard for the size or tolerances of connectors, which means that even if two connectors from different manufacturers look like they are the same size and shape, the imperceptible differences can be real – and damning.
Brian Mills of Stäubli states that intermating connectors is a violation of the National Electrical Code (NEC), but says that it hasn’t stopped many installers from doing exactly this.
“We have turned down customers who wanted to intermate connectors,” Shoals CEO Dean Solon told pv magazine. “We tell them we don’t want to part of the lawsuit.”
MC-4 compatible?
Given that intermating connectors violates NEC and that different connectors from different manufacturers can have imperceptible differences, you’d think that manufacturers would want to be clear that their product cannot be intermated with a product from a different manufacturer.
But that would be forgetting the human weakness of avarice, and how this can short-term long-term interests. Solon and Mills both note that many connectors are described as “MC-4 compatible” on module maker’s data sheets, suggesting to installers that they can be intermated with Stäubli’s MC-4.
“It’s a load of bull****” comments Solon.
And despite clear statements from Stäubli that its warranty will be violated if its connectors are mated with products from other suppliers, this has not stopped the “MC-4 compatible” label.
Shoals says that module makers need to be addressed here, and that when it supplies packages of materials including modules to customers, that it requires suppliers to list full specifications, including naming the manufacturer who made the connectors that are on the modules.
Penny-wise, Pound-foolish
Both Mills and Solon note that the issue with using cheap connectors and/or intermating these to other connectors is somewhat absurd, given how little connectors add to the overall cost of modules.
“You are talking 1% of the total balance of materials for companies to save to go cheap,” says Dean Solon of Shoals. He says that due to what he describes as stupid errors, his team is currently repowering around 800 MW of solar projects that were installed only a few years ago, including swapping out the electrical balance of systems components.
And while not every connector failure results in a fire, there are real hazards – including for installers. “They don’t understand that the interconnections in a PV system are the highest risk points,” points out Mills.
“The amount of energy that exists at that point is tremendous. It’s an order of magnitude higher than anything you are going to encounter in your home, it’s DC connection, and it’s outside.”
Shoals’ Dean Solon notes that this could also lead to major legal issues. “The first time somebody is electrocuted, the lawyers are going to be the happiest people in the room.”
Dean Solon, Brian Mills and Jan Mastny of LEONi will be discussing how to avoid fires, including issues with connectors, at pv magazine’s Quality Roundtable at the Solar Power International trade show in Salt Lake City on September 25. Attendance is free to those with SPI passes. Click here to learn more about this event and to register.
This content is protected by copyright and may not be reused. If you want to cooperate with us and would like to reuse some of our content, please contact: editors@pv-magazine.com.
You would think that panels would be shipped with a black covering so they cannot electrocute the installer.
The panels do not electrocute the installer. This is about connectors.
Wow. I thought all these connectors were standardized. They should be. I have noticed that the quality of different makers is very different. But all the connectors I have seen look very much the same and interconnect.
Big problem there folks. Better do something ASAP.
i live in zephyrhills fl. how do i get your magazine ?.
https://shop.pv-magazine.com/
For decades, Belden and Switchcraft freely provided all the tech info installers needed to insure their products would not fail when attached properly. In my commercial experience there’s no standard training to insure that every installer learns how to properly strip and crimp solderless connectors. Belden says “7 out of 7”, meaning not one stranded wire winds up on the client’s floor. Switchcraft precisely defines the differential scales of the approved crimper, AND the circumference of the wire and/or connector involved.
In reality, 5 out of 7 ‘pro-installers’ are using cheap wire strippers to crimp what is supposed to be a “gas-tight” perfect union. “Lossy” performance is no joke when you multiply the error with each parallel string.