The US Inflation Reduction Act (IRA), signed into law in August 2022 by US President Joe Biden, greatly expands incentives to deploy clean energy and includes a new set of production tax credits for domestic solar, battery, and wind manufacturing. As a result, many companies, including newcomers, have announced US factories which are sorely needed to meet expected demand. The question remains, however, whether manufacturing facilities will ramp fast enough and, if not, where the gaps will be and how dependent US solar will remain on Southeast Asian imports.
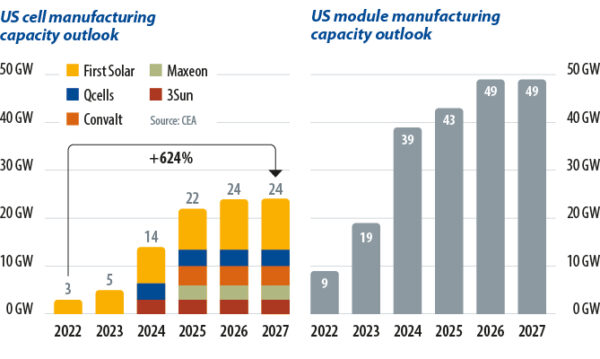
According to the US Solar Market Insight Q3 2022 report published by Wood Mackenzie and the Solar Energy Industries Association (SEIA), US solar generation capacity could rise from 129 GW today to 335 GW in 2027.
While installations fell in 2022, mostly due to Uyghur Forced Labor Prevention Act trade issues, the US Department of Energy’s (DOE) Energy Information Administration expects the solar market to rebound, with 29.1 GW to be added in 2023. That would more than double the 2021 utility-scale record of 13.4 GW.
How much?
The DOE’s “Solar Futures Study” predicts aggressive cost reduction, supportive policy, and large-scale electrification will mean solar could supply 40% of US electricity in 2035, and 45% in 2050. That would require average annual growth of 30 GW in new solar capacity this year and next, rising to 60 GW extra per year from 2025 to 2030, for a terawatt of new solar capacity by 2035.
The IRA delivers the supportive policy needed to increase domestic manufacturing by way of an advanced manufacturing tax credit, known as Section 45X, which provides tax incentives for specific manufactured goods produced and sold in the United States. The credit lasts through 2029 and then begins to phase down.
The IRA offers “quite generous incentives” along the entire supply chain for manufacturers, said Christian Roselund in a recent pv magazine webinar. Roselund, senior policy analyst at US solar and battery supply chain management business Clean Energy Associates (CEA), said it costs $0.245/W of generation capacity to ship a Southeast Asian solar module to the United States. It cost $0.35/W to make a module in the US before the IRA, Roselund said, but now “suddenly, it costs $0.18 a watt.”
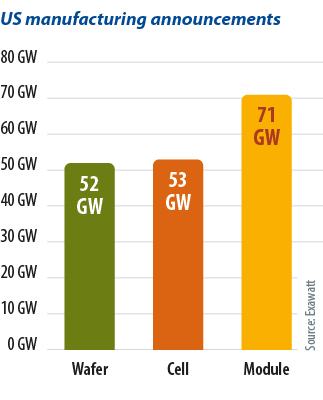
Many manufacturers have announced their intent to begin producing modules in the US and some have promised more upstream supplies, such as cells, wafers, ingots, and polysilicon.
South Korea’s Qcells plans to build it all. The company has announced it will invest more than $2.5 billion to bring fully integrated solar manufacturing to the US. Considered the largest solar investment in US history, it will make the business – a subsidiary of conglomerate Hanwha Group – the first to establish a facility to manufacture 3.3 GW of solar ingots, wafers, cells, and modules annually. The company estimates it will be producing 8.4 GW of product in Dalton, Georgia, by 2024.
Alex Barrows, head of PV at UK-based solar consultant Exawatt, believes 60 GW of manufacturing capacity is possible but admits it is too early to say if it will come to fruition. Italian business Enel Green Power, for example, is planning a 3 GW-per-year heterojunction solar cell and module facility at an undisclosed US location which, the energy company says, will scale to 6 GW.
Barrows said 30 GW of US module production capacity “should be achievable” based on confirmed announcements. The Exawatt analyst noted it’s likely module manufacturing will achieve 60 GW but ingot, wafer, and cell production will lag. Barrows said the cell capacity planned thus far is part of the integrated strategy of Qcells, Enel, and others that plan to manufacture a similar level of around 10 GW. Cells produced by vertically integrated manufacturers are unlikely to be available to other module makers.
Key challenges
Despite the IRA incentives luring manufacturers to set up shop in the US, several challenges remain to ramping up domestic production across the supply chain. Michael Parr, executive director of Washington DC-based trade body the Ultra-Low Carbon Solar Alliance, says making polysilicon, wafers, and cells is capital intensive and that is why we are initially seeing so many announcements that are instead about module manufacturing. Any mismatch between US module and cell production capacity would see module makers remain dependent on imported cells for the foreseeable future.
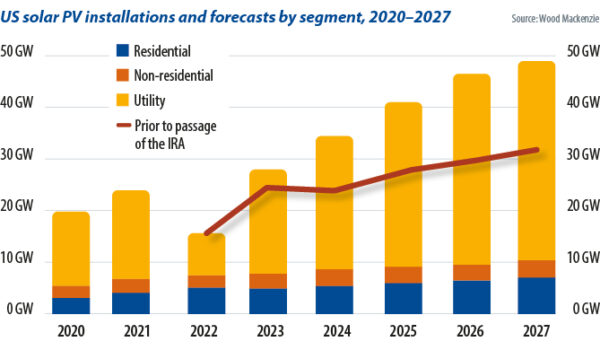
Further upstream
If imports from China are not considered, Parr says, the US is short on wafer supply. “If you want a domestic supply chain, wafer is where you want to be,” he says. Parr notes US solar manufacturer CubicPV – formerly 1366 Technologies – is planning domestic wafer production. CubicPV has announced plans for 10 GW of wafer capacity in the United States, driven by IRA incentives, in a move that would create an estimated 1,500 jobs.
There is also a mismatch in anticipated US polysilicon, ingot, and cell production capacity. CEA expects around 30 GW of annual module manufacturing capacity in 2027 but only 3 GW of ingot and wafer lines and 17 GW of polysilicon fabs. Germany’s Wacker Chemie and Michigan-based Hemlock Semiconductor are manufacturing polysilicon in the US, and Norwegian business REC Silicon intends to restart its idled plant in Moses Lake, Washington this year.
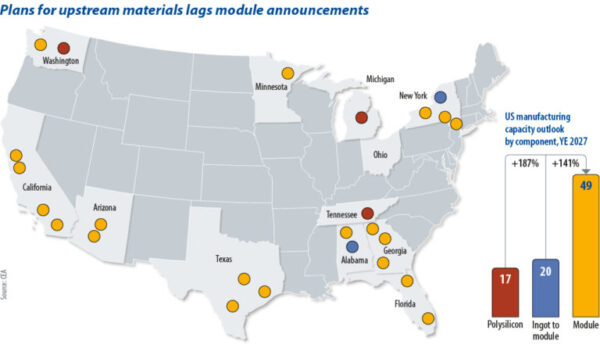
That means significant gaps, CEA’s Roselund says, even if some of the 30 GW module capacity announced includes First Solar’s cadmium telluride products. “There will still be much more module than cell [manufacturing]” he adds.
Ingot manufacturing faces similar challenges and no construction has started to date, despite announced plans for production lines. Roselund says it could be challenging for ingot manufacturers to “reach the capacities they’re talking about.” He explains that there are not many players in the area that have extensive, recent experience in making ingots and wafers using industry-standard production methods.
Relying on imports
Even if the United States does achieve 60 GW of polysilicon, ingot, wafer, cell, and module production capacity, it will still be importing various other materials including glass, frames, and junction boxes.
As Exawatt’s Barrows notes, “you would still be likely to rely on imports, within the supply chain, to some extent.” With the nation likely to reach that figure only in terms of annual module manufacturing capacity, Barrows says the key challenge is that US manufacturing is “meaningfully more expensive than manufacturing in SE [Southeast] Asia – labor and capex [capital expenditure] in particular.”
Referring to the practice of slapping trade tariffs on solar imports, though, Barrows says production incentives will have a role, adding, “Realistically, we know that tariffs alone won’t work – you need both a carrot and a stick.”
With some module imports likely to be necessary to meet US solar demand, CEA’s Roselund says the big manufacturers in SE Asia are developing Uyghur forced-labor-prevention-compliant modules and, “generally speaking … that value chain is adapting to requirements of US trade law.”
This content is protected by copyright and may not be reused. If you want to cooperate with us and would like to reuse some of our content, please contact: editors@pv-magazine.com.
By submitting this form you agree to pv magazine using your data for the purposes of publishing your comment.
Your personal data will only be disclosed or otherwise transmitted to third parties for the purposes of spam filtering or if this is necessary for technical maintenance of the website. Any other transfer to third parties will not take place unless this is justified on the basis of applicable data protection regulations or if pv magazine is legally obliged to do so.
You may revoke this consent at any time with effect for the future, in which case your personal data will be deleted immediately. Otherwise, your data will be deleted if pv magazine has processed your request or the purpose of data storage is fulfilled.
Further information on data privacy can be found in our Data Protection Policy.