Climate change and energy crises continue to dominate headlines and exert pressure to produce clean energy alternatives to fossil fuels. With policy developments in the United States, such as the passage of the Inflation Reduction Act, investments in domestic manufacturing appear to be set to grow at an unprecedented pace as manufacturers work to meet the moment with expanded capacity.
From a production standpoint, the key to enabling this growth efficiently and sustainably lies in digital transformations for scalable and cost-effective manufacturing of solar energy components. Let’s examine the hyperautomation and digital twin initiative we undertook at First Solar (Nasdaq: FSLR), for a master class in how the industry can optimize production, drive cost per watt down and shorten energy payback time.
Factory of the future
All manufacturers struggle with modern challenges that include pandemic-related production slowdowns, talent shortages, high sourcing costs and overall supply chain upheaval. For solar technology manufacturers like First Solar, the last two years have prompted a pivot away from the legacy approach of hub-based manufacturing and towards the strategic siting of new manufacturing capacity close to demand.
In such a pivot, competitiveness is enabled by enhanced efficiencies, which, in turn, require digital transformation and automation to modernize the solar manufacturing environment. This was the goal of First Solar, the only U.S.-headquartered company among the world’s ten largest solar manufacturers and a leading global manufacturer of advanced thin film photovoltaic (PV) technology. With a fully vertically integrated manufacturing process that is among the most advanced and efficient in the solar manufacturing industry, First Solar is uniquely suited to further embrace digital transformation to create a “factory of the future.”
A factory of the future is founded on breaking down information silos and streamlining the flow of data – from the shop floor to the top floor – to enhance visibility and intelligent decision support across all manufacturing and operations. Organizations that succeed in this create what’s known as digital thread, a seamless flow of data that runs through the entire organization.
Digital thread, in turn, brings to life digital twins. These virtual replicas of physical operations are finely detailed and exact in mirroring and predicting impacts to any contemplated changes in workflows, machinery, controls and systems. Mature digital twin capabilities can support virtual commissioning and emulation of PLC codes, immersive instruction and training visualizations for equipment operators, advanced design prototyping, and other capabilities that optimize production.
These advantages are amplified in solar production. That’s because panel manufacturing is mid-to-high volume, with processes and workflows that First Solar sought to optimize through faster cycle times, higher cascade yields and industry leading tact times. Production flow throughout the factory is critical to achieve peak throughput, and First Solar saw an opportunity to leverage virtual testing of layout design and control strategies to maximize production throughput.
With the help of Kalypso, First Solar laid out a strategy to leverage digital twin and related smart manufacturing systems for a more connected, data-intensive operation that would provide unprecedented visibility and control around production flow of current and future operations. Added capabilities include advanced analysis of production data to predict and prevent issues; closed-loop auto-resolution of production anomalies; and enhanced visualizations like immersive virtual reality (VR) tools to streamline collaboration and triaging of issues.
Real-world benefits
The digital transformation efforts, including the benefits of digital twins, enabled First Solar’s efforts to scale manufacturing of responsibly produced PV modules that support America’s transition to a decarbonized future. This helps First Solar improve productivity while achieving significantly lower costs, waste, and energy payback times.
To fully understand the application and benefits of the technology, the Kalypso team worked with First Solar to develop and deploy a digital twin pilot to a bottleneck part of an existing factory that was being retooled. A digital twin was used to simulate infeed/outfeed and material handling of the area including identifying optimum routing of the solar panels and placement of a buffer to maximize production output. This model also helped test multiple scenarios and proactively anticipate bottlenecks in the area. All of this was done virtually using a digital twin that replicated production line scenarios.
Based on outcomes of the pilot phase, a digital twin is being developed to optimize operations across First Solar’s newest manufacturing factory in Ohio, which is expected to come online in the first half of 2023. Virtual modeling helps inform production layout and processes for all 20 manufacturing zones that make up the factory – optimizing everything from workflows and equipment placement to materials transfer, maintenance cycles and more. Throughout, First Solar uses “copy smart” factory scaling techniques to ensure manufacturing of solar modules is done with the same process and equipment in each factory, yielding the same results no matter where a particular module is made.
Innovation at a critical moment
The solar industry is at an inflection point as the sector navigates a confluence of external conditions. The combination of demand driven by the economics of solar, long-term policy, and the urgency of climate change is driving activity across the industry and its value chains. However, it is essential that this growth is sustainable, efficient and capable of not just meeting the moment today, but of addressing tomorrow’s needs with high quality, competitive manufacturing and supply chains.
Fortunately, digital twins and other digital initiatives for intelligent operations are here to help in solving these pivotal challenges of efficiency and scale – strengthening a solar manufacturer’s handling of everything from responsible manufacturing and product performance, all the way to end-of-life management and recycling.
As First Solar has shown through its own pioneering efforts, digital twin capabilities translate into lower costs, reduced waste, and vastly improved productivity – all of which helps the solar industry rise to the occasion.
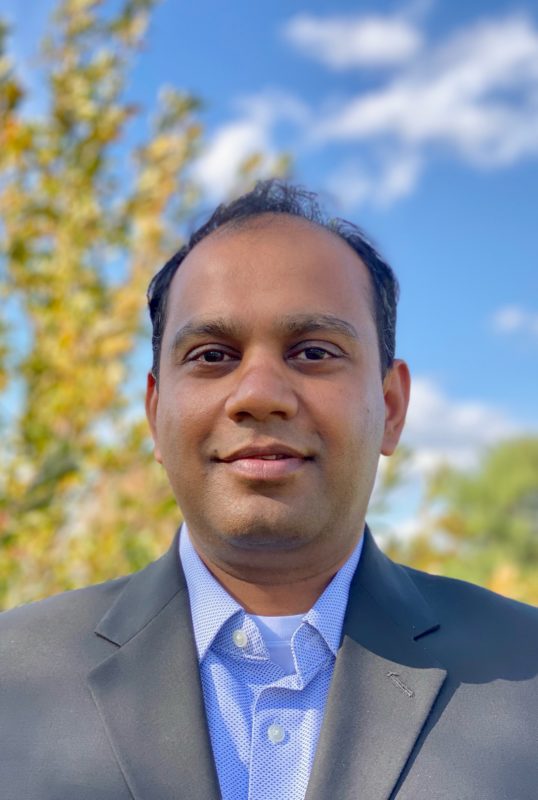
Image: First Solar
Jay Mehta is the head of global manufacturing engineering at First Solar, and is responsible for setting the automation roadmap and new technology direction for First Solar manufacturing. Jay has more than 16 years of experience in high-tech manufacturing including prior experience in Semiconductor manufacturing.
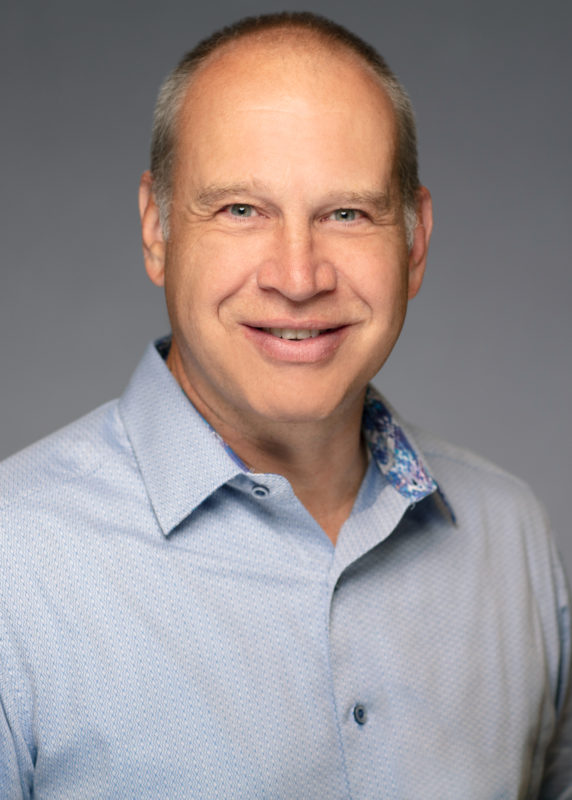
Image: Kalypso
Chad Markle is principal, global commercial lead at Kalypso. Chad has over 25 years of experience working as an executive and advisor in technology-driven industries to deliver results by combining strategic thinking with the transformative business impact of technology. He leads the global commercial operations for the entire Kalypso business across industries, capabilities and geographies; helps clients to achieve digital transformation of the value chain; and works to build the future leaders of Kalypso.
The views and opinions expressed in this article are the author’s own, and do not necessarily reflect those held by pv magazine.
This content is protected by copyright and may not be reused. If you want to cooperate with us and would like to reuse some of our content, please contact: editors@pv-magazine.com.
By submitting this form you agree to pv magazine using your data for the purposes of publishing your comment.
Your personal data will only be disclosed or otherwise transmitted to third parties for the purposes of spam filtering or if this is necessary for technical maintenance of the website. Any other transfer to third parties will not take place unless this is justified on the basis of applicable data protection regulations or if pv magazine is legally obliged to do so.
You may revoke this consent at any time with effect for the future, in which case your personal data will be deleted immediately. Otherwise, your data will be deleted if pv magazine has processed your request or the purpose of data storage is fulfilled.
Further information on data privacy can be found in our Data Protection Policy.