Three manufacturers, Merlin Solar, Solarge, and LG, are making a move away from the standard aluminum and glass solar panel in a bid to lower weight, emissions, and cost.
The product from Merlin Solar has been found recently on yachts in pv magazine USA. Its value is that, first, it isn’t a standard framed product and so can be attached directly to a flat surface. Second, due to its unique busbar technology, the product is able to be walked on without damage.
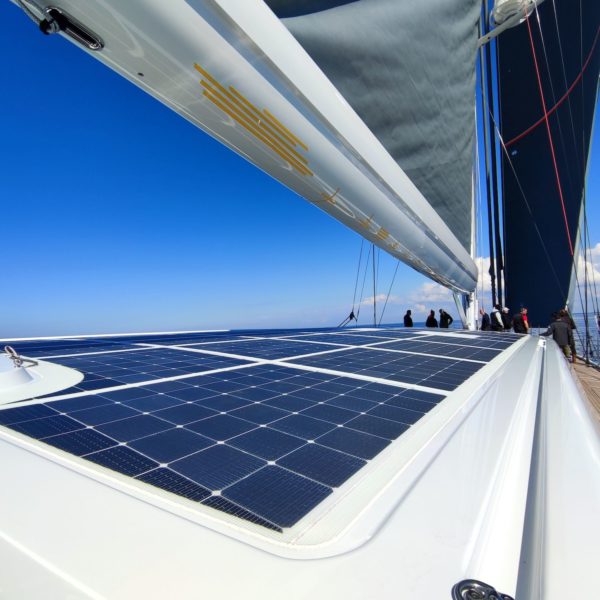
Merlin Solar’s main goal, however, is to place its product on top of commercial structures whose limited available collateral load — the amount of weight that can be added to a structure’s roof and meet local building code regulations — doesn’t allow for the pounds per square foot (3-7 psf) that a standard solar installation requires.
The company recently installed 550 kWdc of its product on an oil storage tank in Rensselaer, New York. Merlin Solar said this site could neither take on the additional weight, nor gain owner approval for an attachment technique that might puncture the structure’s outer roofing layer.
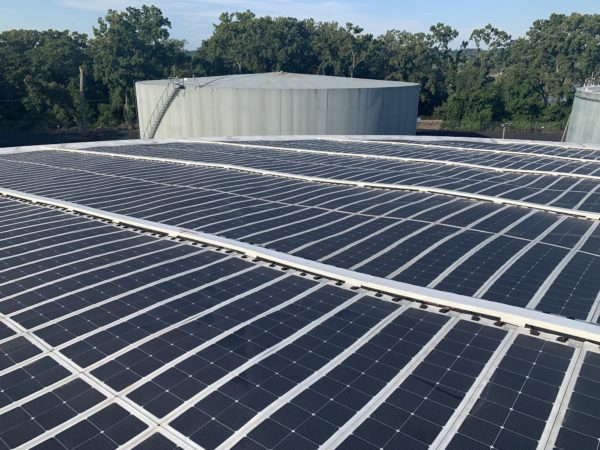
Merlin Solar also markets its product in a framed format where a stronger structural attachment is required, or where a more rigid solar panel is desired. Even so, the product weighs considerably less than a standard solar panel because it does not use a glass front shield.
Solarge has released a product that replaces the glass of a solar panel with a plastic product. Currently, the company is manufacturing the panel on a pilot line which it said it hopes to scale up by the end of 2022. The company’s panel can be bought on its own, or as part of their custom designed east-west facing rooftop racking product.
The solar panel weighs just under 32 pounds (14.5 kg). For comparison’s sake, a Q Cell product made in Georgia weighs 43.8 pounds (19.9 kg). In the east-west configuration and including the racking hardware, the Solarge DUO will weigh 1.35 psf (6.6 kg/m2). And keep in mind that the lowest allowable collateral load often is around 3 psf.
One point emphasized by the manufacturer is the product’s apparent strong emissions and recyclability credibility:
The product will have a CO2 footprint which is 80% lower than conventional solar panels and the panel is completely circular in design and uses no Per- and polyfluoroalkyl substances (PFAS) materials, unlike all other solar panels that use a polymeric film instead of glass.
LG Chem — part of the conglomerate that also sells the successful LG solar panel line with a manufacturing facility in Alabama — has announced that it is exploring turning the frames of solar panels from aluminum into plastics.
LG Chem said the product is as strong as aluminum, but cheaper and, of course, lightweight. Although no specific numbers were available, an LG Chem press release said its product can be manufactured with post-consumer recycled polycarbonate which will lower the emissions of the frame.
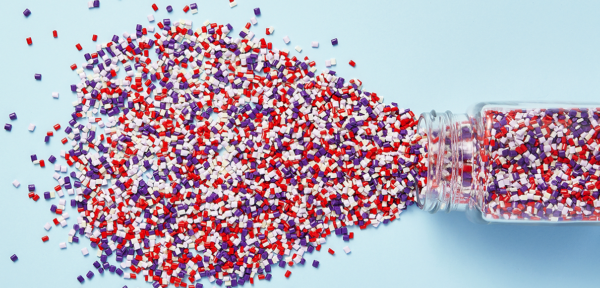
Image: LG Chem
The compound, called LUPOY EU5201, is an engineering plastic composed of ASA (Acrylonitrile Styrene Acrylate) resins with polycarbonate as a base, and reinforced with glass fibers. High rooftop temperatures are well tolerated by the compound, which incorporates a flame retardant. It can maintain its shape across a range of temperature due to its low coefficient of thermal expansion. And LG Chem claimed the new compound is highly resistant to corrosion, resistant to impacts, and extremely resistant to UV.
The company said it began selling products in the third quarter, indicating that it could already be headed toward solar panel factories for final manufacturing.
Plastics?
A shift to more plastics in solar panels will gain the attention of those who are considering the environmental credibility of solar power. While aluminum and glass manufacturing use an immense amount of energy, plastics are a major contributor to global trash pollution. They also are manufactured from hydrocarbons (oil).
However, the actual manufacturing of plastics from hydrocarbons — a process called cracking — doesn’t release emissions. It is the energy used to generate the heat — usually from fossil gas — that results in greenhouse gas emissions.
From this author’s experience building rooftop solar power, access to products that would lower the psf by greater than 50% of what is often our lowest allowable collateral load of 3 psf would open up a large amount of rooftop space for development.
This content is protected by copyright and may not be reused. If you want to cooperate with us and would like to reuse some of our content, please contact: editors@pv-magazine.com.
Plastic does have a bad rep due to the trash pollution, but this is definitely a step in the right direction especially if the industry can take advantage. If LG Chem is saying the product is as strong as aluminum, but cheaper and, of course, lightweight, Plastic may be the new go to especially if it provides the same value at a lower cost.
Like the author John F. Weaver states, It seems there is a lot to look forward to especially for commercial solar..
“..rooftop solar power, access to products that would lower the psf by greater than 50% of what is often our lowest allowable collateral load of 3 psf would open up a large amount of rooftop space for development.”
On a house rooftop I would be concerned about fading over a 30+ year life. Non-UV plastics (and a lot of claimed UV resistant plastics) have a bad reputation because in 5 years they fade and become brittle. This is especially true in places where solar makes the most sense – TX, AZ, NV. Here in Colorado we have a mile less of atmosphere to filter the UV through.
Hope it works out for everyone – cheaper, lighter panels would be great.
What’s the impact on the need for earthing of solar panels where they have plastic frames? Does it lower the risks associated with a lightning strike, or electrical fault?
What kind of material is ideal for constructing a hot house or a greenhouse?
The polycarbonate twin wall sheet is one of the most effective materials for greenhouse construction. It is nearly impossible to break and provides thermal insulation that is up to sixty percent more effective than that of greenhouse glass or PVC film. Very user-friendly for do-it-yourself projects and more affordable than glass. Because of the positive effects that light has on your plants.
What materials should be utilized to construct a greenhouse?
Twin-wall polycarbonate sheet is frequently cited as one of the best materials to utilize for constructing greenhouses. Compared to PVC film and greenhouse glass, it retains heat up to 60% better and lasts a long time. This material is frequently utilized since it is more accessible and more convenient to work with than glass. Plants grow stronger and healthier when exposed to sunlight.