It happens every day: A bird flies over your rooftop solar panel array and deposits an unwelcome offering on a cell. The bird dropping is an annoyance that needs to be cleaned off. But it also can result in a hot spot on the affected cell, impacting the entire panel’s output and potentially affecting its long-term performance.
The phenomenon is known as reverse bias and the hot spot that is its hallmark is something of an Achilles Heel for the solar industry. That’s because a single cell weakened by a bird dropping or a leaf shadow can be overpowered by stronger cells that surround it. Those neighboring cells send a reverse flow through the weaker cell causing it to experience temperatures that can exceed 400F and operate at voltages in excess of 20 times those of forward voltages.
All of that leads to cell stress, premature aging, and the increased likelihood of a module’s total failure.
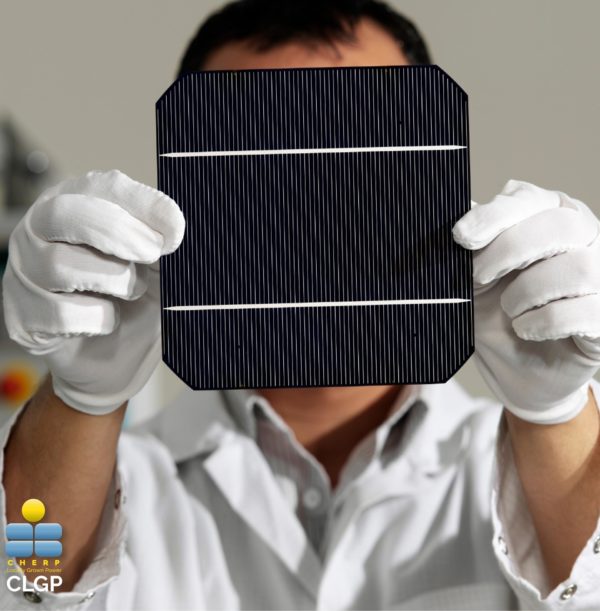
A serial inventor, Kent Kernahan, first began to tackle the problem more than a decade ago. His solution was to design a control technology that detects reverse bias and redirects current away from the affected cell and through the rest of the otherwise healthy solar panel. He went on to create a company, IdealPV, to develop the technology.
And here’s where things get even more interesting: he also established a business model that could help disadvantaged communities all across the U.S. by making the technology available to non-profit entities set up under Section 501(c)3 of the U.S. tax code. The first such non-profit to start manufacturing IdealPV solar cells is getting underway now in California. More on that in a bit.
Call for help
At its core, the control technology that Kernahan developed watches for a signal that the weakened cell sends out as it begins to overheat. The control system uses that signal to throttle back the affected cell, redirect current across the panel, and ease the onset of a reverse bias event.
“The breakthrough allows us to anticipate reverse bias” and act to alleviate the emerging hot spot, Kernahan told pv magazine in a recent interview.
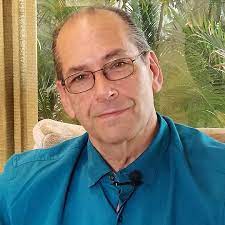
IdealPV’s solar panel technology is based on what Kernahan refers to as the Law of Forward Only Zero Hot Spot (FOZHS). Derived from the First Law of Thermodynamics and the Law of the Photoelectric effect, FOZHS lays out that the conductance of a solar cell falls as its voltage becomes more negative. The company’s solar panels make practical use of this insight to keep the conductance of each solar cell high and prevent any of them from being subjected to the reverse (negative) voltage that drives extreme heat into the cell.
Unwinding the process
In and of itself, that’s a useful advancement in cell design. But Kernahan sees broader implications for his innovation across the cell manufacturing value chain. Because most modules are designed to manage wide variations in temperatures across very small intervals, everything from glass to adhesion and backsheeting is designed to handle temperature extremes.
By addressing reverse bias and the resulting heat, Kernahan and IdealPV moved to unwind and rethink the entire module manufacturing process. For example, without the need of bypass diodes and buss bars, it becomes practical to put more, shorter cells in series. This reduces internal cell and panel currents and increases internal panel voltage. In turn, this allows for cells with corner chips, local AR defects, and cracks to be used. Such cells typically are a fraction the cost of cells without defects.
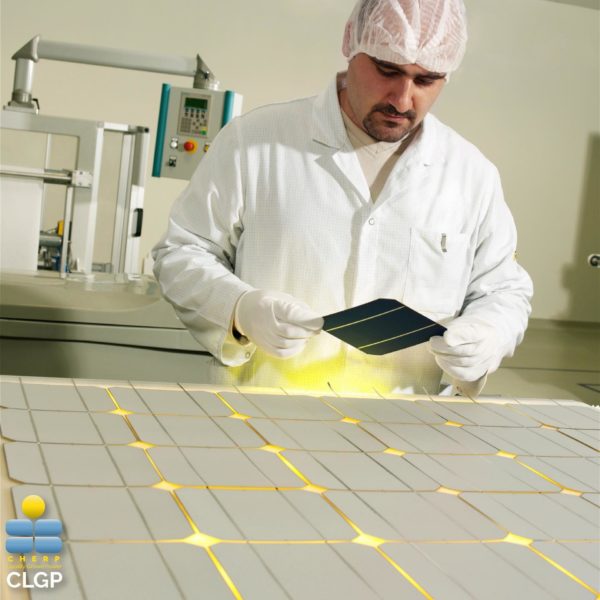
The ability to remove heat-related design parameters “dumbs down the manufacturing requirements,” Kerhahan said, making for a “very forgiving manufacturing process.”
And that opens the door for what Kernahan and others hope will be a nationwide network of nonprofit solar module manufacturing facilities. By making use of provisions within the U.S. tax code, a group known as Community Home Energy Retrofit Project (CHERP) is working with individual and corporate investors whose focus is not on shareholder returns and maximizing profits, but on an underlying social mission to work in disadvantaged communities and expand solar’s adoption among low- and moderate-income people.
The first factory dedicated to IdealPV solar cell production opened in Claremont, California, earlier this year. Made possible in part by $2.1 million from the California state budget, the factory is waiting on certifications for its solar panel from the National Testing Laboratories. Once those certifications are in hand, CHERP will start to hire with a goal of producing its first modules later this year.
The factory will create around 200 jobs, with entry-level warehouse and installation workers paid between $16 and $20 per hour. Each panel produces around 330KWh a year through its expected 25-year production life. Each will cost about $160 to build and take around 45 minutes to assemble. The plant will be able to produce up to 105,000 panels a year or enough for about 6,000 typical Southern California households. The switch to solar is projected to save those residents a combined $6.5 million in energy costs yearly.
Once the first facility is up and running, the plan is to replicate the template nationwide and help other community-based non-profit group create manufacturing jobs and deploy solar. Talks are under way with a substance abuse recovery facility in West Virginia, a green sustainability initiative in Michigan, and a gang rehabilitation and re-entry program in Los Angeles.
The initial goal of taking the heat out of solar panels could lead to the emergence of a non-profit-based solar manufacturing sector, Kernahan said. “We want to bring back middle-class employment and manufacturing.”
This content is protected by copyright and may not be reused. If you want to cooperate with us and would like to reuse some of our content, please contact: editors@pv-magazine.com.
It sounds like a great idea, and the community benefit is cool. So why obscure the actual costs with numbers that don’t match the industry? If I pick a location, say Los Angeles, PVWatts tells me that 330kWh/year is roughly the output of a 200W panel, which the article says will cost $160 to make, so $0.80/W. There are social benefits, and maybe reliability benefits, and costs will likely come down, but it sure seems like the article was written to avoid mentioning that number.
Yes, a social conscience is a fine thing in business, and to be encouraged. One question : If existing PV manufacturers mimic this hotspot tech, would they not simply incorporate the subgrade cells in their products, rather than selling them off cheaply? That would destroy any secondary manufacturers that relied on them.