Underscoring what some call the solar industry’s “systemic overestimation bias,” kWh Analytics found that the average solar asset underperformed its target weather-adjusted production by 6.3% between 2016 and 2019 (early life); one-quarter of the projects that were studied missed their production targets by more than 10% after accounting for weather.
These data points are unsettling, but are they surprising? After all, what accounts for the industry’s overly optimistic bias towards over production?
In short, self-interest. When the developer, EPC company, and long-term owner are all financially motivated to assume generous production, they generally will. The inevitability of real-world data crashing this party was bound to happen.
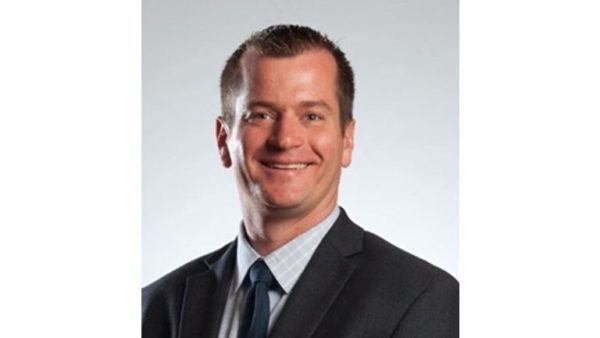
A recent IEA renewables report reiterates how solar has evolved beyond being an accessory in the nation’s energy mix to being the lowest-cost, highest-growth energy generation source going forward.
This inflection point represents an opportunity for the industry to shift its attention away from constant cost-out and toward putting our collective effort into building projects that reliably generate cost-effective clean energy.
The ever-increasing deployment of solar assets can’t be contained. For the health of the whole industry, we owe it to ourselves to deploy better projects.
Three factors
Beyond the kWh Analytics tools, there are three main areas every solar industry participant needs to be mindful of to help assure that projects meet projections.
Production Estimates – or why 0.5% annual degradation rates are almost always wrong. Early in my solar career, I proudly said that products from the company I worked for out-performed production estimates by 10%. Someone wisely told me that if that was true, we should fire our modeler.
While many independent engineers and owners rep services provide third-party validation of production models, the single-input, single-output principle of any analytic tool holds true for solar. If everyone uses the same flawed project assumptions, then the outputs will be flawed. Reality always has a way of showing up poor models.
Although made more challenging due to the pandemic, site visits are critical to validate not just shading and azimuth, but also actual site conditions.
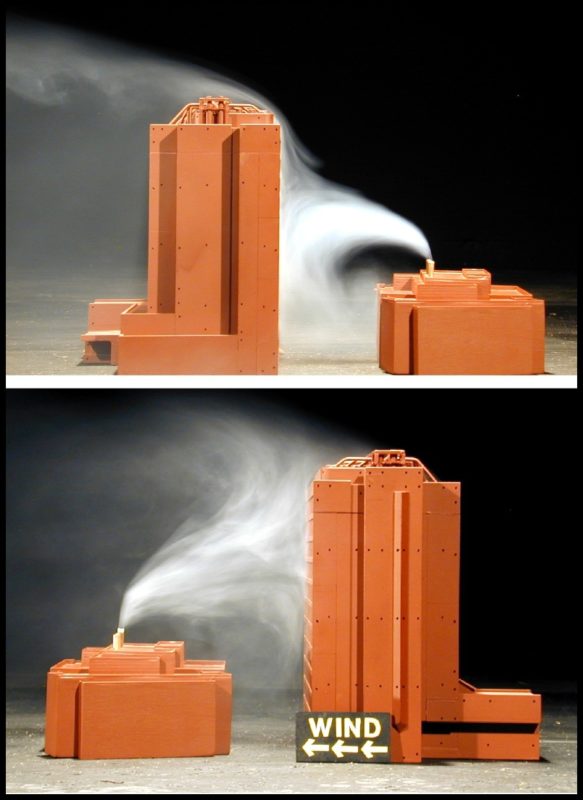
Image: NREL
I’ve seen unshaded rooftop arrays vastly underperform models thanks to exhaust from a neighboring factory that was not worked into project model’s soiling rate. I’ve also seen the production model on a utility-scale field not account for a high-voltage transmission line that ran right over the center of the array because it wasn’t visible on Google Earth.
Some of the most common production estimate mistakes come from relying too much on system defaults. It doesn’t matter if those estimates are produced by PV Syst, Helioscope, or even PV Watts. Module and inverter companies publish data sheets and simulation files – often audited by third parties – informed by real-world performance and test data. And those third-party-validated simulation files must be used for accurate modeling.
For example, in the majority of system simulations, they assume too often that every module degrades at 0.5% per year, including the first year. Specifying a high-efficiency module could improve that degradation rate from 0.5% to as little 0.35 or 0.25% per year.
So, what may seem like an incremental improvement at best may result in end-of-life performance as much as 10% higher than with a typical commodity solar module, and that translates into real production value.
Performance Risks in Construction. While large-scale arrays are typically closely inspected around PTO (permission to operate), these inspections may miss damage caused during installation that’s not otherwise visible.
An extreme example is construction crews walking on modules, leaving micro-cracks. Trust me, this happens more than anyone wants to admit.
Then there are easily found but often missed inter-mating of mismatched connectors and poor wire management, which can cause arcs and faults. Or, torque a clamp too tightly on a module and it can create compression on the frame, leading to a premature failure that isn’t typically covered by a warranty and which might not manifest itself as a visual failure until after a year or two of production.
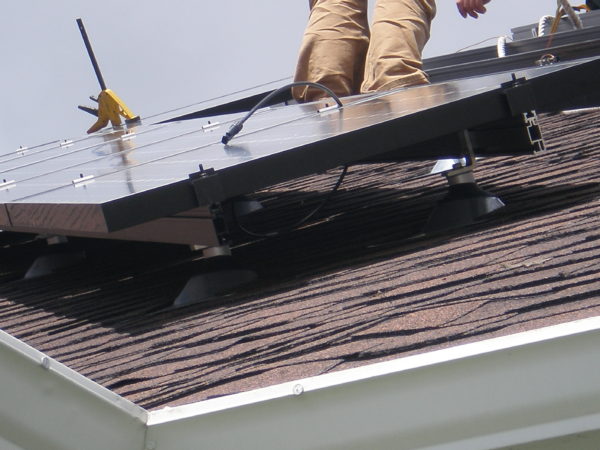
Image: NREL/Susan Bilo
A significant construction-related risk factor in system underperformance is the selection of lowest-cost components whose performance doesn’t match model expectations. While independent factory auditors can help assess and mitigate this risk, they often are looking more for adherence to quality standards and a certain bill of material. These factory audits don’t entirely mitigate the risk of a serial failure in a sub-component, such as a backsheet or connector.
I don’t know the extent to which the system underperformance tracked by kWh Analytics was due to premature component failure, but it likely was more than failing to properly quantify soiling rates.
No one knows what component will fail in 5 or 10 years. But everyone can assess the viability of the manufacturer to be able to honor warranty claims. Metrics such as BNEF’s “Tier 1” are an important tool to help guide companies toward reputable firms. Those metrics, however, shouldn’t be used as a reliable predictor of product quality or a company’s financial health without further validation and due diligence.
O&M — or, how we can learn to love the OpEx. If a project’s upfront modeling was accurate and if the EPC built a quality project using high-performance material, then it’s operations and maintenance (O&M) that may make or break an array’s long-term performance.
We’ve all stared at the same Excel spreadsheet trying to hit a certain hurdle rate. And we’ve all worked to squeeze every penny out of the CapEx. Now it comes time to shaving dollars off the OpEx by reducing the scope of work on your O&M provider.
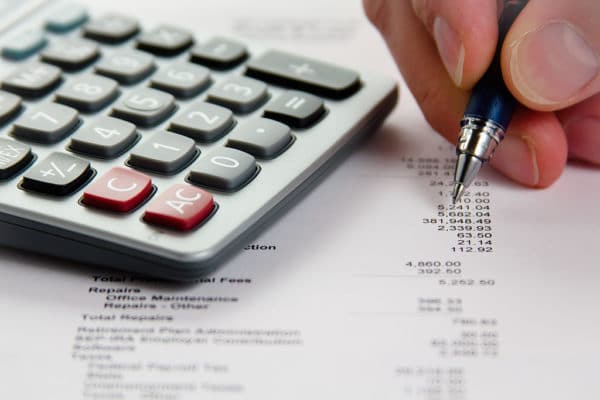
Image: Wikimedia Commons/Dave Dougdale
The likely result of reducing the O&M expense is reducing the O&M service, which may have an outsized impact on long-term power generation.
Frankly, saving a dollar on O&M that impacts system performance by a percentage point for the last 10 years of an array’s service life doesn’t really make sense for the long-term asset owner.
Long-term owners need to invest in quality O&M, and they should audit to ensure the work is done to agreed-upon standards. Good O&M is more than cleaning off modules and running inverter checks. It extends to performing preventive maintenance to ensure long-term reliable clean power generation from the asset.
Reliable solar asset performance for the long term relies on three disciplines: proper project development, quality EPC work and thorough O&M. All should be spot-on to ensure solar assets reliably perform for their contractual lifespan.
While remaining mindful of cost, the industry must now pivot from focusing on short-term cost reductions to developing, building, and maintaining long-term value and performance.
Industry veteran Brian Lynch leads U.S. solar business development for LG Business Solutions, the B2B division of LG Electronics USA.
The views and opinions expressed in this article are the author’s own, and do not necessarily reflect those held by pv magazine.
This content is protected by copyright and may not be reused. If you want to cooperate with us and would like to reuse some of our content, please contact: editors@pv-magazine.com.
By submitting this form you agree to pv magazine using your data for the purposes of publishing your comment.
Your personal data will only be disclosed or otherwise transmitted to third parties for the purposes of spam filtering or if this is necessary for technical maintenance of the website. Any other transfer to third parties will not take place unless this is justified on the basis of applicable data protection regulations or if pv magazine is legally obliged to do so.
You may revoke this consent at any time with effect for the future, in which case your personal data will be deleted immediately. Otherwise, your data will be deleted if pv magazine has processed your request or the purpose of data storage is fulfilled.
Further information on data privacy can be found in our Data Protection Policy.