Active Surfaces, a Massachusetts-based startup spun out of MIT, has raised $5.6 million in an oversubscribed pre-seed funding round led by Safar Partners, a deep tech venture capital fund.
Active Surfaces is developing lightweight, flexible solar panels that can be integrated into virtually any surface. The solar is manufactured using a printed, roll-to-roll process. Co-founder and CTO, Richard Swartwout, said that this funding will enable the company to expand R&D efforts, scale up production, and bring its “cutting-edge solar solutions to market more rapidly”.
The funding round was led by the deep tech venture capital fund Safar Partners. Additional participants include QVT, Lendlease, Type One Ventures, Umami Capital, Sabanci Climate Ventures, New Climate Ventures, SeaX Ventures, and others—reflect a diverse support base ranging from institutional VCs to corporate backers.
“Active Surfaces is pioneering a transformation in the built environment,” said Tommaso Boralevi, Technology & Innovation Director Europe at the Milan Innovation District (MIND) established by Lendlease, a global construction, development, and investment company. “At Lendlease, we are committed to advancing sustainable urbanization, and our investment in Active Surfaces represents a significant step towards integrating novel capabilities directly into the fabric of future developments.”
The company was also awarded $100,000 as part of last year’s MIT $100K Entrepreneurship competition. It had previously won $75,000 from Massachusetts Clean Energy Center’s (MassCEC) Catalyst, Diversity in Cleantech – Early Stage (DICES), and InnovateMass programs that support clean energy and climatetech innovators in Massachusetts.
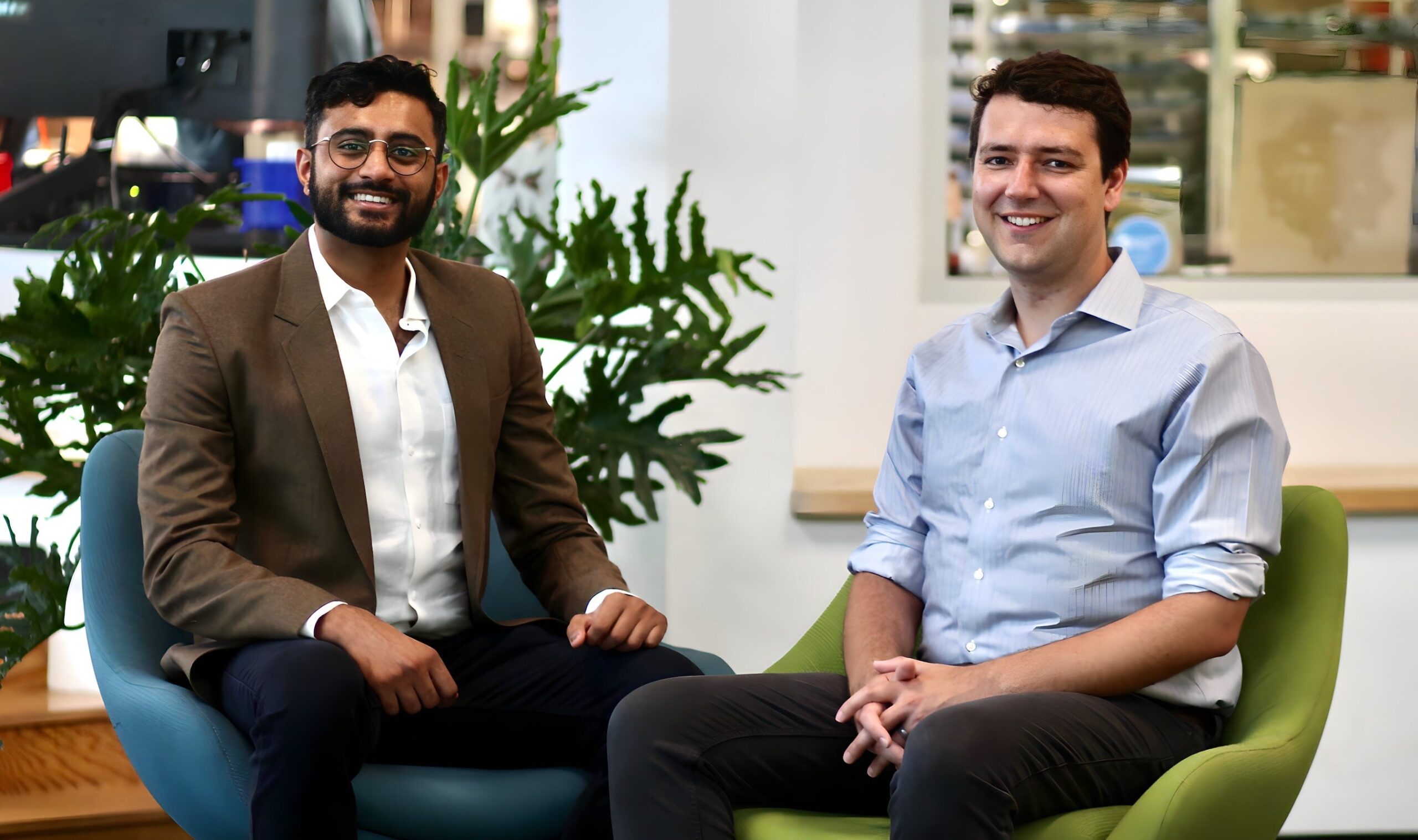
Image: Active Surfaces
Swartwout describes the flexible, thin film solar as a “solar 2.0” technology. Solar 1.0 technology is seen in the large, rigid and heavy solar panels commonly installed today. Active Surfaces expects its solar 2.0 thin-film solar to deliver dramatically higher efficiency, lower costs and greater versatility.
The company plans to scale its laboratory-fabricated 4-by-4-inch photovoltaic devices by advancing industrial roll-to-roll semiconductor printing technologies.
The process originally began in the MIT.nano clean room, where a team of researchers coated the solar cell structure using a slot-die coater. This deposited layers of electronic materials onto a 3-micron thick substrate. Then an electrode is screen printed onto the structure. The module, which is then about 15 microns thick, can be peeled off the substrate.
The choice of substrate was critical as it had to be lightweight and flexible, yet strong. What they found was a composite fabric known as Dyneema, made of extremely strong fibers. A UV-curable is added in a thin layer, which adheres the solar modules to the fabric to form what is described an an ultra-light and mechanically robust solar structure.
By adding a layer of UV-curable glue, which is only a few microns thick, they adhere the solar modules to sheets of this fabric. This forms an ultra-light and mechanically robust solar structure.
This content is protected by copyright and may not be reused. If you want to cooperate with us and would like to reuse some of our content, please contact: editors@pv-magazine.com.
By submitting this form you agree to pv magazine using your data for the purposes of publishing your comment.
Your personal data will only be disclosed or otherwise transmitted to third parties for the purposes of spam filtering or if this is necessary for technical maintenance of the website. Any other transfer to third parties will not take place unless this is justified on the basis of applicable data protection regulations or if pv magazine is legally obliged to do so.
You may revoke this consent at any time with effect for the future, in which case your personal data will be deleted immediately. Otherwise, your data will be deleted if pv magazine has processed your request or the purpose of data storage is fulfilled.
Further information on data privacy can be found in our Data Protection Policy.