Valmont Industries announced the completion of a 718 kW ground mount solar installation that uses Valmont Solar’s own Convert-1P tracker. The energy generated by the system is expected to avoid 400 tons of carbon emissions, offsetting 100% of emissions from the manufacturing of concrete utility poles in the Bristol, Indiana facility.
Valmont partnered with Ameresco, a cleantech integrator and renewable energy asset developer, to build the solar array.
“As part of the long-term need for critical infrastructure investment, we recognize the vital role transmission, distribution and substation structures will play in the energy transition super cycle as well as the importance of sustainability in the products, services and solutions we deliver that conserve resources and improve life,” said Aaron Schapper, president of Valmont Infrastructure.”
The solar modules are mounted on 70 Convert single-axis solar trackers. Valmont acquired the Convert tracker business in 2018 when it took at 75% stake in the company.
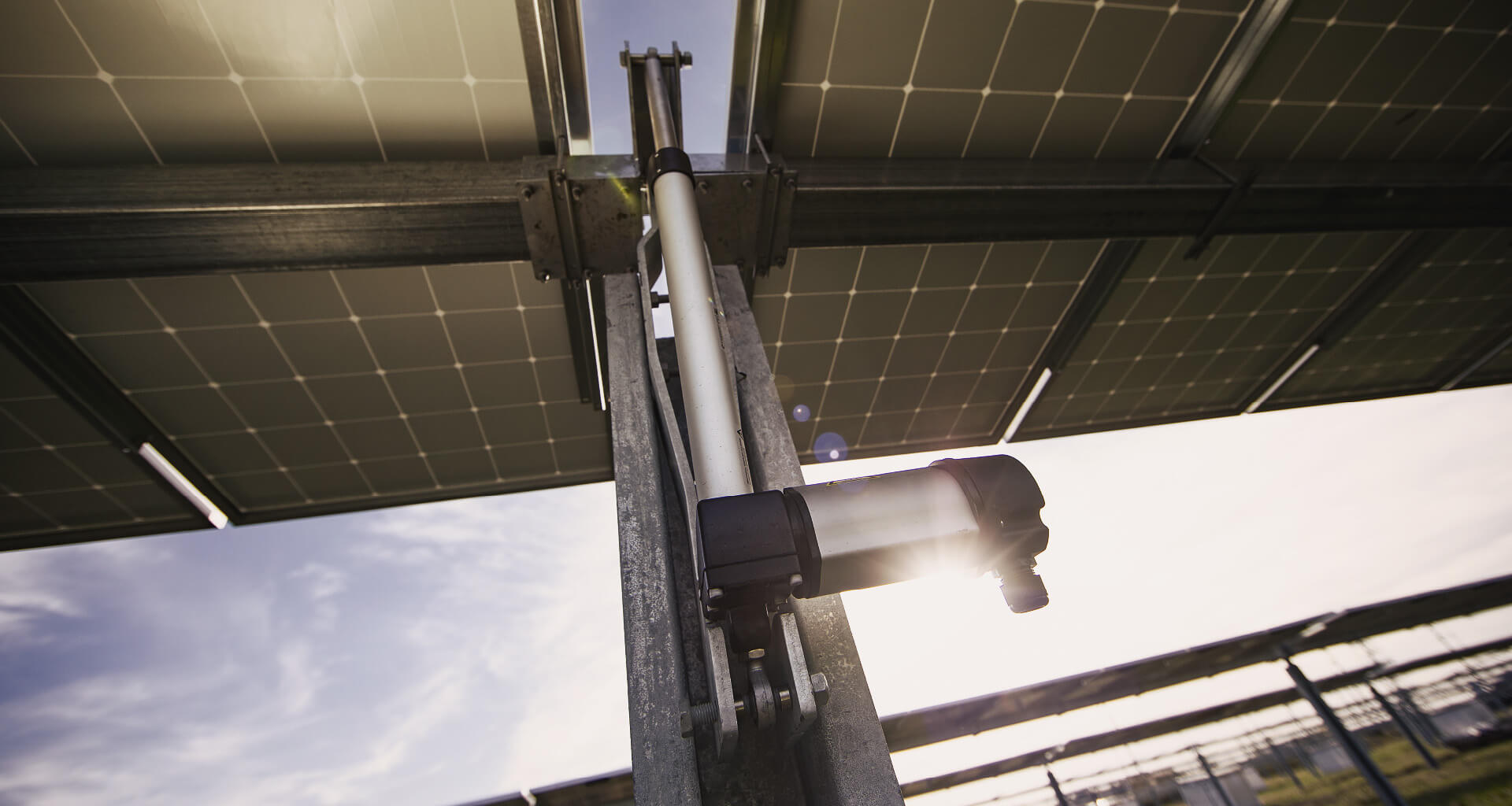
Image: Valmont
The 1P tracker is reportedly optimized to adapt to the topography of the land, and is designed for use in utility-scale as well as distributed generation installations.
In addition to solar, Valmont is taking other steps to reduce emissions in its manufacturing process. The facility is incorporating a concrete mix that uses supplemental cementious materials of steel slag, such as waste material from furnace-burned steel production. Traditional cement production is known as a carbon-intensive process, 90% of which are from the kiln where limestone and silica (shale and sand) are heated to create the material called “clinker” necessary in making cement. Of those emissions, 60% comes from “process emissions,” or the chemical decomposition of limestone in kiln. The other 30% comes from the combustion of fossil fuels to reach the high temperatures required to continually make cement, according to the Department of Energy.
After having been used for decades, Valmont reports that slag cement has proven to be strong and sustainable. According to the company, however, it has never been used at scale in utility pole production. Valmont plans to fully transition all six of its concrete utility pole facilities across the country to the eco-concrete mixture within the next 12 months. The company estimates that the rollout could reduce carbon emissions by 12,000 tons annually across these manufacturing facilities.
“Grid hardening has fundamentally changed the utility pole market and we are innovating with a sustainably focused mindset to meet the demand,” Schapper said.
This content is protected by copyright and may not be reused. If you want to cooperate with us and would like to reuse some of our content, please contact: editors@pv-magazine.com.
By submitting this form you agree to pv magazine using your data for the purposes of publishing your comment.
Your personal data will only be disclosed or otherwise transmitted to third parties for the purposes of spam filtering or if this is necessary for technical maintenance of the website. Any other transfer to third parties will not take place unless this is justified on the basis of applicable data protection regulations or if pv magazine is legally obliged to do so.
You may revoke this consent at any time with effect for the future, in which case your personal data will be deleted immediately. Otherwise, your data will be deleted if pv magazine has processed your request or the purpose of data storage is fulfilled.
Further information on data privacy can be found in our Data Protection Policy.