Each year solar technical advisory and inspection servicer Heliovolta releases a report on solar performance and safety called the SolarGrade PV Health Report.
The report assesses PV health using over 60,000 data points, ranging from projects from 100 kW to 350 MW in size. About 73% of the assessed projects in this year’s report are located on commercial rooftops, 25% are ground-mounted, and 2% are solar carports. All projects are located in the United States.
Heliovolta found some important problem areas for the performance and safety of these solar assets. A staggering 62% of inspected projects were identified to have critical or major issues. Of this share of projects with critical risks, 91% of the major issues were found to be in DC distribution components.
“Issues can be fixed before they become hazardous. Periodic inspections and proactive O&M — especially in the DC distribution section of PV systems — are critical to safe and reliable operations,” said the report.
Heliovolta noted that inverters often appear to be the cause of PV system problems due to the fact they are typically the primary device of energy yield data and error messages. However, on-the-ground data reveals that inverters are rarely the root cause of downtime. In most cases, inverters trip because they detect underlying issues located within the DC Distribution section, said the report.
The report shared that 74% of issues were in the DC distribution section, 9% in racking, 7% in modules, and 7% in inverters.
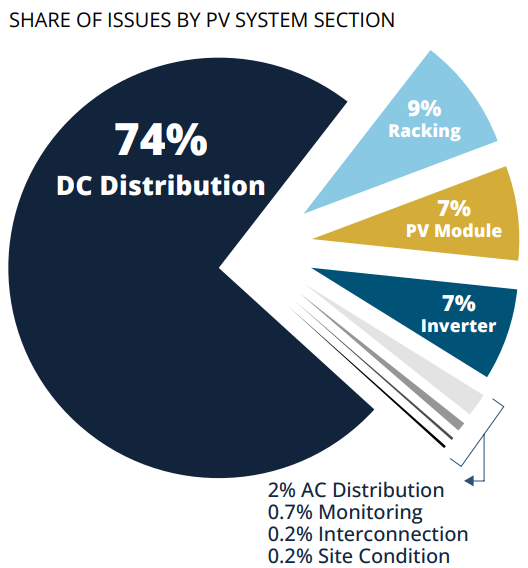
Within this critical DC distribution system failure are a few specific components driving most of the problems. Over 33% of failures in this system were due to field-made PV connectors. Wire management issues were the second cause of failures and safety issues, about 26% of reported problems. Other problems with conduits, raceways, improper installation, combiner boxes, grounding, and wire terminations were listed as significant risks.
(Read: “Solar assets are underperforming expectations by 8%, what is the root cause?”)
“The most frequently observed issues are related to field-made connectors and wire management. Installer error is typically the root cause for these categories of issue — not defective equipment,” said Heliovolta.
The company said that 79% of all field-made connector issues are caused by improper installation or cross-mating of incompatible parts. Identifying and remediating compromised field-made connectors is critical to safety as they can trigger PV system fires by overheating and by creating arc and ground fault conditions. Heliovolta offers a safety guide to solar connectors.
Interestingly, the report found that 37% of all inverter issues were sourced from one inverter provider. This brand was kept anonymous by Heliovolta in the report.
As for solar module performance, about 30% of problems were related to microcracking. These small cracks restrict the flow of current, reducing energy yield and potentially creating hotspots over time. The report recommends using electroluminescent (EL) imagining tests to detect microcracking.
Heliovolta operates a cloud-based software platform called SolarGrade to help manage the performance and safety inspection process. The company’s report recommended five best practices to ensure a more reliable, productive, and safe solar facility:
1) Require robust installer training
DC distribution issues related to connectors and wire management are the most common problems at project sites. With better training protocols, the vast majority of these issues could be avoided.
2) Conduct QA/WC inspections at commissioning
Assessing EPC workmanship through QA/QC inspections early in a project’s lifecycle helps ensure that latent issues are corrected before catastrophic failures occur.
3) Require inspections during operations and maintenance visits twice a year
Periodically walking project sites to assess PV system health ensures that signs of latent component failure and accelerated degradation are identified early.
4) Standardize inspection processes
Make sure inspectors know what to look for in PV system health assessments by providing standardized, accessible, and easy-to-use guidelines. The SolarGrade platform comes with pre-written templates and issue descriptions.
5) Track issue resolution
Do not allow issues to get lost in the shuffle of PDF reports, spreadsheets, and clunky manual checklists. The SolarGrade platform allows field technicians to quickly find problems on the ground, and asset managers can dynamically track issue resolution in the cloud.
This content is protected by copyright and may not be reused. If you want to cooperate with us and would like to reuse some of our content, please contact: editors@pv-magazine.com.
By submitting this form you agree to pv magazine using your data for the purposes of publishing your comment.
Your personal data will only be disclosed or otherwise transmitted to third parties for the purposes of spam filtering or if this is necessary for technical maintenance of the website. Any other transfer to third parties will not take place unless this is justified on the basis of applicable data protection regulations or if pv magazine is legally obliged to do so.
You may revoke this consent at any time with effect for the future, in which case your personal data will be deleted immediately. Otherwise, your data will be deleted if pv magazine has processed your request or the purpose of data storage is fulfilled.
Further information on data privacy can be found in our Data Protection Policy.