Following the passage of the Inflation Reduction Act (IRA), an energized solar industry is aiming high and envisioning a future where the United States has a robust domestic energy supply chain. The Solar Energy Industries Association (SEIA) released a roadmap to achieving this goal, with a target of 50 GW of annual solar manufacturing capacity by 2030.
The United States has been plagued by numerous pressures threatening the supply of solar modules imported from overseas. With decarbonization and climate goals under threat due to this shortage, the U.S. is now turning to boosting domestic manufacturing to power the energy transition.
The Department of Energy (DOE) said, “Greatly expanding U.S. PV manufacturing could mitigate global supply chain challenges and lead to tremendous benefits for the climate as well as for U.S. workers, employers and the economy.” DOE concluded in a study that U.S. production could reach 10 GW in two years, 15 GW in three years and 25 GW in five years on its path to 50 GW annual production.
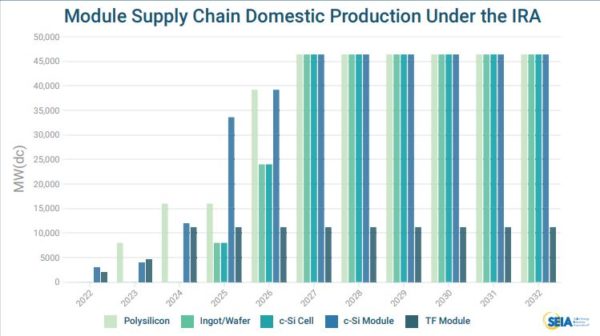
Titled Catalyzing American Solar Manufacturing, the report explores how the U.S. can move from its current state of limited production to a full-fledged, economy-powering domestic energy supply chain.
Currently, the U.S. has capacity to produce materials like metallurgical grade silicon, polysilicon, steel, aluminum, resins, racking and mountings. However, there are significant gaps in the supply chain. United States currently has no domestic solar ingot, wafer or cell manufacturing capacity and only modest capacity to produce solar modules, inverters and trackers, said SEIA. As a result, these segments must be targeted on the path to 50 GW.
The SEIA report said with the right application of new IRA incentives the U.S. should be on track to meet, or even exceed, the 50 GW goal across all segments of the solar supply chain.
Domestic manufacturers should focus on building downstream production first and backfilling components with imports while upstream domestic production is built out, said the report. While scaling domestic module capacity will take 2-3 years, it will be 3-5 years before there is significant domestic manufacturing capacity for ingots, wafers and cells.
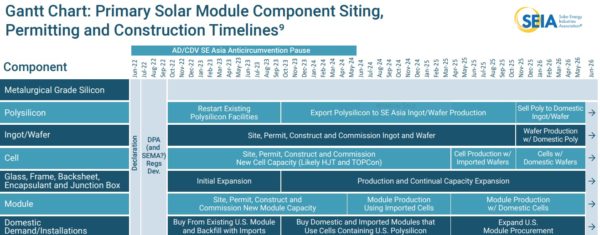
SEIA said investments in manufacturing should be timed intelligently and with awareness of demand. As an example, scaling solar ingot and wafer operations before new domestic cell capacity comes online could potentially strand new investments. The importance of domestic raw material supplies, and funding for related environmental impact assessments also cannot be overlooked. For example, building new domestic solar glass capacity will significantly improve the cost competitiveness of U.S. module assembly.
U.S. manufacturers must create in-demand products, by selling at a competitive price and delivering quality goods. This cost competitiveness will likely only be achieved at large-scale, which requires significant upfront investment, said the report.
Following the IRA, groundbreakings for large-scale manufacturing facilities will likely commence in 2023, and the first new factories supported by these policies will begin production in 2025, or as early as 2024 for trackers, racking and aggressive inverter and module manufacturing investments.
A successful buildout will require a robust U.S. workforce. The report said this will depends upon collaboration between companies, government agencies and higher education institutions; to advance solar-specific technical training and college-to-career programs. Diversity, equity, inclusion and justice should be central to the workforce strategy of the energy transition.
SEIA offered nine pitfalls to avoid on this path:
- Failing to go big
-
- The United States requires a core group of mega-factories able to compete globally. Small factories should focus on niche markets.
-
- Setting aside economies of scale, utility-scale developers need suppliers with capacities at least four times their project size. For someone building a 350 megawatt (MW) solar power plant, that means at least 1.4 GW of USP module capacity.
- Building out the supply chain in the wrong order
- Building factories dependent on obsolete production equipment, or that are dependent on obsolete or soon to be obsolete technology (efficiency and automation are key to producing cost-effective and quality products)
- Only incentivizing capital expenditures (CapEx):
-
- CapEx is an important hurdle, but it is only a fraction of a product’s cost when considered over long-term horizon (polysilicon is an exception).
- Federal tax incentives that are difficult to monetize, particularly for domestic manufacturers. Tax credit policy should include a way to facilitate monetization.
- Only paying attention to high-tech components or end products:
-
- Solar manufacturing is not just module manufacturing
-
- There are many components critical to a solar project and many inputs critical to a component
- Not providing long-term investments focused on demand certainty, CapEx support and ongoing production support
- Targeting technologies that are not commercially ready:
-
- Need to focus on building leading-edge technologies commercially available for when factories come online. For crystalline silicon wafers, that means larger wafer formats. For solar cells and modules, this likely means heterojunction and TOPCon.
-
- Essential to continue research and demonstration for more advanced technologies, but companies should not focus large-scale manufacturing on unproven technologies.
- Other issues to avoid:
-
- Failure to consider building and siting challenges, e.g., permitting, access to roads, electricity access, etc. There are parallels between building a factory and the challenges in building utility-scale solar projects around land use and environmental impact. For example, it should not be assumed that everyone wants to see a new factory in their area or that they know what goes on in a factory
The full report can be read here.
This content is protected by copyright and may not be reused. If you want to cooperate with us and would like to reuse some of our content, please contact: editors@pv-magazine.com.
By submitting this form you agree to pv magazine using your data for the purposes of publishing your comment.
Your personal data will only be disclosed or otherwise transmitted to third parties for the purposes of spam filtering or if this is necessary for technical maintenance of the website. Any other transfer to third parties will not take place unless this is justified on the basis of applicable data protection regulations or if pv magazine is legally obliged to do so.
You may revoke this consent at any time with effect for the future, in which case your personal data will be deleted immediately. Otherwise, your data will be deleted if pv magazine has processed your request or the purpose of data storage is fulfilled.
Further information on data privacy can be found in our Data Protection Policy.