In September, the United States Department of Energy released the Solar Futures Study which outlines how solar energy could produce 45% of the nation’s electricity by 2050.
In order to reach this target, the U.S. would need to deploy 1,570 GW of solar by that date. The target also hinges on the existence of a concerted policy effort, aggressive cost-reductions, extensive deployment of other clean technologies, and expansions of the transmission system, as well as large-scale electrification of end uses.
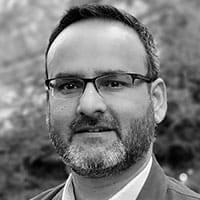
Research and development is vital to maintaining or, ideally, accelerating solar photovoltaic technology cost-reduction trajectories for continued industry growth. There is a particular opportunity for the U.S. to establish itself as a global leader and achieve national decarbonization goals by supporting domestic manufacturing of next generation solar cell technologies.
The next great race
For several years, crystalline silicon solar cells have dominated the market and have become the industry standard against which all alternatives are compared. In 2019, about 83% of the total PV market in the United States was crystalline silicon-based products. Under the umbrella of crystalline silicon cells, monocrystalline p-type passivated emitter and rear cells (PERC) undisputedly dominate the market.
PERC cells are expected to reach an efficiency plateau at around 24% in mass production. With mass production efficiency approaching 23%, PERC seems to be approaching its limits of possible efficiency and performance enhancements. PERC will continue to play a major role in PV deployment in the coming years as manufacturers attempt to close the gap between actual and maximum efficiency. But the race to overtake PERC is already well underway.
The successor to PERC is yet to be determined but it’s safe to say that it will be based on one of the high efficiency n-type-based cells that help overcome the limitations of p-type-based cells. Reports indicate that the market share for n-type cells could grow to 28% in 2028 from barely 5% in 2021.
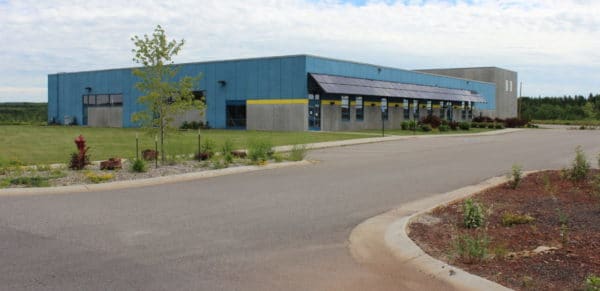
Image: Heliene
One such limitation of the p-type cell is bifaciality, or the ratio of rear efficiency in relation to the front efficiency subject to the same irradiance. The introduction of bifacial technology has enabled higher energy generation from solar systems. The ease with which monofacial PERC cells can be converted to bifacial has contributed to the PERC’s dominance in the market.
But PERC’s bifaciality is limited to roughly 75%, while n-type cells can achieve more than 90% bifaciality depending on the cell structure.
Another limitation of the p-type cell is its high temperature coefficient, which reduces the performance of the modules when operating at higher temperatures. PERC cells have temperature coefficients of power in the range of 0.35%/oC to 0.40%/oC. N-type wafer-based cells inherently have lower temperature coefficients.
N-type cell technologies
There are two main n-type cell technologies: Tunnel Oxide Passivated Contacts (TOPCon) and Heterojunction (HJT). Both technologies have the potential to exceed 25% efficiency in mass manufacturing, with HJT having the potential to go even further.
TOPCon cell manufacturing involves depositing a nanometer scale layer of silicon oxide, followed by a thicker polycrystalline silicon layer, between the silicon wafer and metal contacts. Because the cell architectures are so similar, TOPCon cells can be made by upgrading existing PERC mass production lines with relatively small equipment expense. This gives TOPCon an edge in terms of ease of manufacturing expansion over other n-type cell technologies.
HJT cell manufacturing involves deposition of an amorphous layer of silicon on both the top and bottom of the wafer followed by transparent conducting oxide deposition and making of metal contacts. HJT cell manufacturing consists of significantly fewer steps than PERC or TOPCon.
However, HJT cell production lines are currently more expensive than TOPCon and have to be newly built. HJT cells also use more expensive metallization paste. HJT cells are by nature bifacial, with bifaciality rates above 90 percent, the highest of any cell technology. Temperature coefficient of power of HJT cells is in the range of 0.25%/oC to 0.30%/oC. Higher bifaciality and lower temperature coefficients result in higher energy output compared to TOPCon cells. HJT cells in mass production are expected to reach about 27%.
Tandem cell R&D
One of the most interesting developments in the solar industry is the research and development of tandem cells using HJT as the bottom cell. Laboratory efficiencies of 29% have been obtained using these cells, making HJT cells even more advantageous than TOPCon cells.
As things stand, HJT cells are more expensive to produce than TOPCon cells. This explains the embrace of TOPCon technology by utility-scale solar developers, who are more sensitive to price increases. HJT technology has started to be more regularly adopted by residential and light commercial installers because they address property owners’ demands for enhanced aesthetics, higher durability and increased output.
While HJT modules may currently have a higher initial price tag, property owners are willing to pay for the superior performance and longer lifespan.
Massive opportunity
Remember the Solar Futures Study’s 2050 goal of 1,570 GW solar deployment? We are roughly at 110 GW in cumulative deployment, which is less than 1% of the needed deployment over the next three decades. The U.S. gave up solar innovation and manufacturing leadership more than a decade ago; the tariffs on foreign imports over this period did nothing to bring it back. The good news is, HJT cell (and module) development presents a tremendous opportunity for the U.S. to regain solar leadership.
HJT technology fills an existing innovation gap in the residential and commercial rooftop PV market, which today entirely consists of standard crystalline silicon modules. With additional policy support, HJT modules can provide the required cost reductions to drive continued growth beyond rooftops and into the utility scale segment.
For these reasons, the U.S. would benefit from scaling domestic manufacturing of HJT solar cells and modules. In doing so, the U.S. can reclaim leadership in solar cell technology and achieve ambitious decarbonization goals.
Policies like the Solar Energy Manufacturing for America Act, which was recently signed into law under the infrastructure bill, will help reduce the capital intensity of new manufacturing facilities to cost-effectively scale next generation PV cell technologies, boosting U.S. cleantech competitiveness.
Nadeem Haque is chief technology officer at Heliene.
The views and opinions expressed in this article are the author’s own, and do not necessarily reflect those held by pv magazine.
This content is protected by copyright and may not be reused. If you want to cooperate with us and would like to reuse some of our content, please contact: editors@pv-magazine.com.
One critical correction to this opinion piece. SEMA was not part of the infrastructure bill, the latter contains less than $100M in PV specific provisions. Instead most elements of SEMA have been folded into the Build Back Better Act which has passed the House and is presently under consideration in the Senate.