In the last two years, the 210mm wafer has emerged as the clear frontrunner in cell size innovation. It has displaced the previous 156.75mm standard that represented more than 90% of the monocrystalline market, and offers advantages in power output that have allowed module power ratings to exceed 600 W from a 60-cell PERC module.
In an industry where cost is everything, the increase in production capacity brought about by large-size products–reducing the cost of labor, depreciation, and operating, management and financial expenses per unit of output–has promised to significantly cut balance of system costs and the levelized cost of electricity.
Yet, as modules change in size and form factor, ripple effects are felt across the entire solar industry, requiring tweaks, modifications, and outright changes to longstanding project development and construction practices.
Mounting and installation
Perhaps nowhere are these adjustments more impactful than in the module mounting world, especially with regards to trackers. Manufacturers have to take into account and adjust for new size dimensions, weights, and environmental and operational variables presented by a newly dominant module size.
(The 2021 Roundtables USA virtual event November 9 takes on the topic of large-format modules with a panel made up of Longi Solar, Arctech, and Solar Innovations. Register here for this free event.)
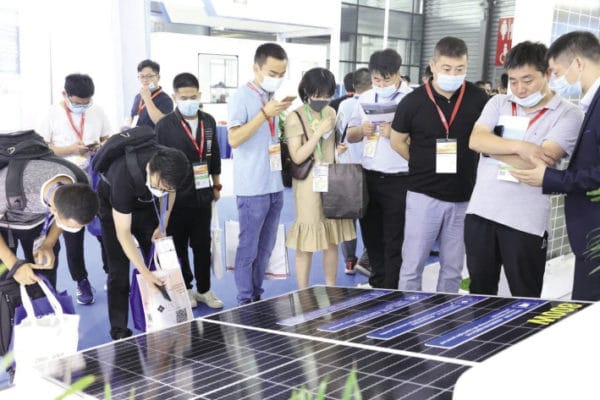
Image: JA Solar
To better understand the challenges that larger modules present to tracker manufacturers in both engineering and installation, pv magazine spoke with experts at two of the industry’s leading companies: Cody Norman, director of applications engineering at Array Technologies, and Nick Mattison, product line manager for NEXTracker’s NX Horizon smart solar tracker.
“Larger PV modules result in higher loads,” Norman said. “These loads are primarily on the module support components, but it’s also on the tracker structure and the foundation.”
Increased load on the tracker presents two distinct challenges: dead weight load across an installed row and dynamic weight in severe wind and weather events. Dead weight has an effect on the tracker by limiting how many modules can be supported by the tracker in a row.
“With modules that are significantly longer, significantly heavier, we might not be able to achieve a full 100-meter row length,” said Norman. “There’s some mechanical limitations of having that much mass supported along the tracker.”
Row-length limitation has been an issue for NEXTracker, one that the company is still working to conquer, said Mattison.
Wind sails
Both said that the majority of mechanical changes have been pushed by the incident pressures of wind and snow on the module.
Larger modules take wind and snow pressures and turn them into higher forces applied against the module and the tracker structure. This factor has required additional analysis that both companies have had to consider during the design process.
“The modules themselves effectively create a sail,” said Mattison “When you increase the size of that sail, that translates to a lot of extra load.”

Image: Array Technologies
To accommodate those forces, Norman said that Array has looked to increase the extent, size, and depth of foundations across the tracker row. It also has turned to using purlins and mounting clamps with more material and more reach.
Wind load is most significant on modules at the end of a row, said Norman. Modules at the exposed end may require additional fasteners to handle the higher wind load forces.
NEXTracker, by contrast, has not added components to bear the static and dynamic loads. Instead, it has opted to “beef up” and reinforce existing hardware, specifically the rails, according to Mattison.
Both said that the tracker drives — the motors which rotate the panels rows to track the sun — were areas of considerable focus. Outside of some adjustments to torque tube layout and position, however, the drives remained essentially unchanged.
Installation strains
As for the installation process, Norman and Mattison both said that it has remained relatively unchanged. The newer, larger modules still require just two workers to install. However, it’s a different story for two-in-portrait (2P) installations where the modules and trackers are higher off the ground.
“You’re managing a module that’s probably five square feet larger and probably 15 pounds heavier, if not more, than what you’re used to working with,” said Norman. “When you’re working well above your head, these heavier, larger modules are kind of challenging to deal with.”
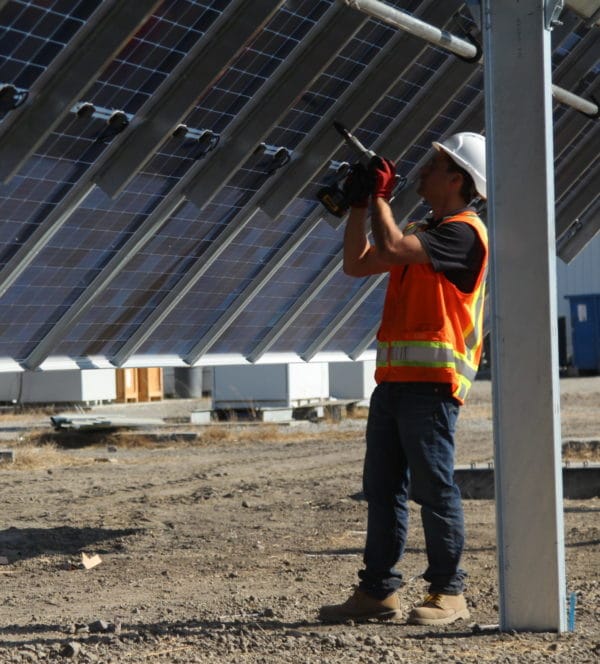
Image: NEXTracker
With the exception of 2P installation concerns, Norman downplayed the challenges these tweaks present, framing them instead as a natural evolution of the technology. To him, the biggest challenge was how quickly 210mm wafer modules became standard across the industry.
It’s not as if either Array or NEXTracker was caught off guard by the new module sizes, far from it. Both Norman and Mattison highlighted how closely their companies collaborate with leading manufacturers.
The issue was that any new standardized form factor needs to go through extensive usage testing, extreme weather resilience testing, and project-level consideration to ensure that the trackers and their hardware are compatible with the new modules in every usage case. Having to accelerate these verification processes was an issue that both companies faced but handled well, according to Mattison and Norman.
Mattison said that NEXTracker has had to test compliance for more than 100 modules that make use of the 210mm cell size.
Standardization
One future issue is standardization. Some in the industry are concerned that module sizes will just keep growing and changing as new innovations become financially viable. The worry is that there is a breaking point in terms of size, as having to add a third installer per module would throw a wrench into labor costs and installation times.
Concerns over size variances are real enough that eight prominent module manufacturers, Risen Energy, Zhonghuan Semiconductor, Tongwei, Trina Solar, Huansheng Photovoltaic, Runyang New Energy Technology, Canadian Solar, and Wuxi Shangji Automation, are pushing to standardize 210mm silicon wafers and modules.
“The 600 W+ sizes that we’re seeing, where they’re 2.4 meters long, 1.3 meters wide, 38 kilos, if we start moving past 40 kilos or 1.5 or larger meters wide, it’s just going to be a major sail,” said Norman. “We’re also going to have to start worrying about the mechanical capabilities of the module itself: how much metal is going to be required in the frame to support the load, how much glass is being used and what’s the thickness?”
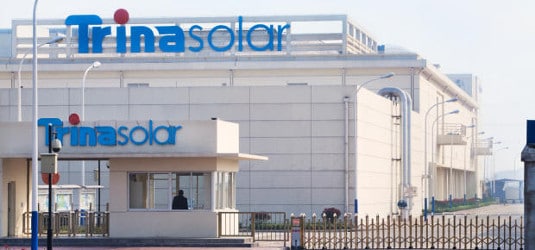
In late October, Trina Solar said the China Photovoltaic Industry Association (CPIA) was set to announce a set of standard dimensions for large format modules relying on the 210mm wafer launched by Zhonghuan Semiconductor in 2019.
Having a standard set of dimensions should make thing simpler, and therefore cheaper, for project developers and component suppliers. All of them have to deal with uncertainty over module sizes and electrical characteristics since the switch to larger wafer formats began to play out.
For Mattison, the idea of standardized wafer and module sizes is one that he would support, although he notes that previous standardization efforts have lagged, and that the market tends to settle into a universal size range.
“A year ago, it was all over the place, but it seems to be consolidating down to just a few form factors now,” Mattison said.
Both solar pros predicted that, at least in the short term, innovation in power density will likely shift toward efficiency, as the sector is nearing the apex the size of modules that two workers can install.
“Where we’re at,” Mattison said, “is probably close to where we’re going to be for the next few years.”
(The 2021 Roundtables USA virtual event November 9 takes on the topic of large-format modules with a panel made up of Longi Solar, Arctech, and Solar Innovations. Register here for this free event.)
This article originally appeared in the October issue of pv magazine’s print publication.
This content is protected by copyright and may not be reused. If you want to cooperate with us and would like to reuse some of our content, please contact: editors@pv-magazine.com.
By submitting this form you agree to pv magazine using your data for the purposes of publishing your comment.
Your personal data will only be disclosed or otherwise transmitted to third parties for the purposes of spam filtering or if this is necessary for technical maintenance of the website. Any other transfer to third parties will not take place unless this is justified on the basis of applicable data protection regulations or if pv magazine is legally obliged to do so.
You may revoke this consent at any time with effect for the future, in which case your personal data will be deleted immediately. Otherwise, your data will be deleted if pv magazine has processed your request or the purpose of data storage is fulfilled.
Further information on data privacy can be found in our Data Protection Policy.