In 1997, the first of REC‘s solar wafers were being hand washed. Today, a highly technical team of professionals monitor and refine the robotic manufacturing processes at facilities in Singapore.
The company sat down with pv magazine at Solar Power International 2018 to educate the market on its newest product, the REC N-Peak Series, but as it turns out the story of the new module is as much one about the company behind it.
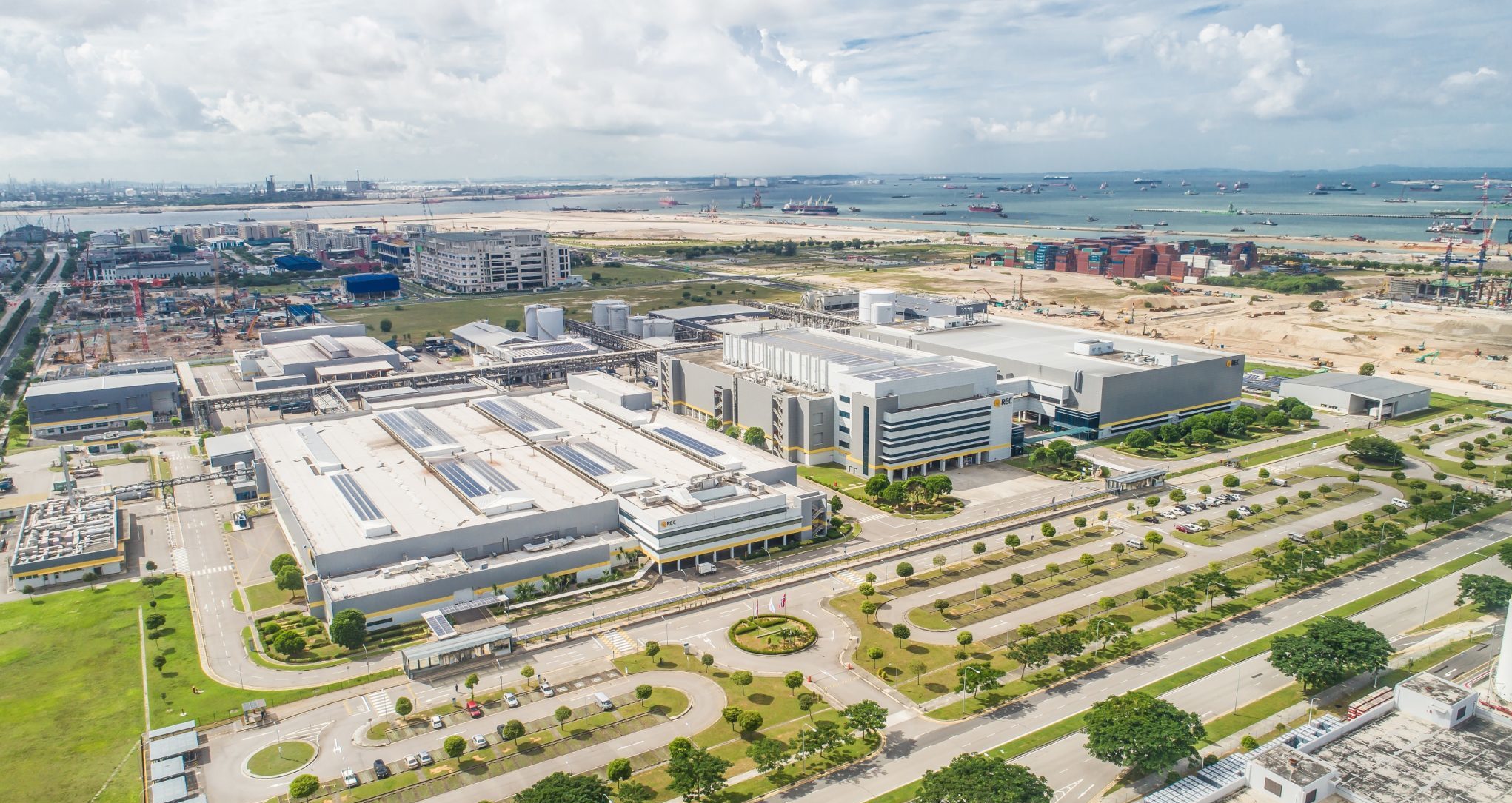
The headline’s purpose was to push your attention to something that would be quaint! To make REC seem endearing, to bring them closer to you – because, bless their hearts, they’re hand washing those wafers! And now you, the solar power professional, have a story to give your customers – about those sweet, hard working folks at that lil ‘ol solar factory.
The reality is of course is that this speaks to the depth of participation, PhDs, machine builders at a 4.0 manufacturing facility, research plus spreadsheets, traceability throughout the supply chain, product return rates around one module per five megawatts, plus a couple of robots that might just have slight personality defects as they unceremoniously, and unrelentingly, shoot hail and stress the structure of these most pristine solar modules. But hand-washed solar wafers are much more cuddly than the cold, hard numbers below.
The REC N-Peak Series (.pdf specification page) ranges from 310 to 330 watts. The company’s “twin” theme started when REC split its modules in two, mostly isolating the top from the bottom sections of the module. Along with the module being split in half, each of the respective halves themselves are have three partially isolated subsections. This allows for increased production in partial shade situations (clouds and trees), tighter ground coverage ratios, and limits the spread of any damage that might collect in the field.
These days, the twin motif goes a bit further with the “split” solar cell technique that lowers resistance and ups module output five to eight watts. REC has been doing this for a number of years, but of late half-cut cells have caught on with a wider range of manufacturers.
The half cut cells are based on N-type monocrystalline wafers with Passivated Emitter Rear Cell (PERC) surface treatment. REC decided N-type was the place to go for them – skipping over P-type products – after buying and testing solar cells of all types. One N-type benefit noted by the company is that due to being ‘doped’ by phosphorous, versus boron in P-type cells, there is no potential induced degradation (PID).
The backside of the module, below right, also shows off twin bars – kinda like sway bars in your car – that shifts the glass from being the heaviest carrier of loads, to the frame. Additionally, there is greater structural strength – 7000 pascals versus the industry standard of 5400 – which also allows REC to make the frame thinner, 30 mm versus 36-42 mm around the industry. This lowers per watt shipping costs by upping volume of modules per pallet and container.
It matters that REC’s pedigree is as a manufacturer of silicon because it means they have the technical ability to look at your solar panel’s journey from the sand it is mined from, to your project site in a very holistic manner. The company currently manufactures around 4 million solar modules per year, and projects that about 160 to 240 of them will come back – a success rate of ~99.995%. REC says this success rate has been consistent for years.
After accepting that, like all things, solar module manufacturing isn’t a perfect enterprise, the company developed a system of ‘traceability’ for every component. This allows for ‘root cause analysis’, as the silicon can be traced backwards to the block it originated from.
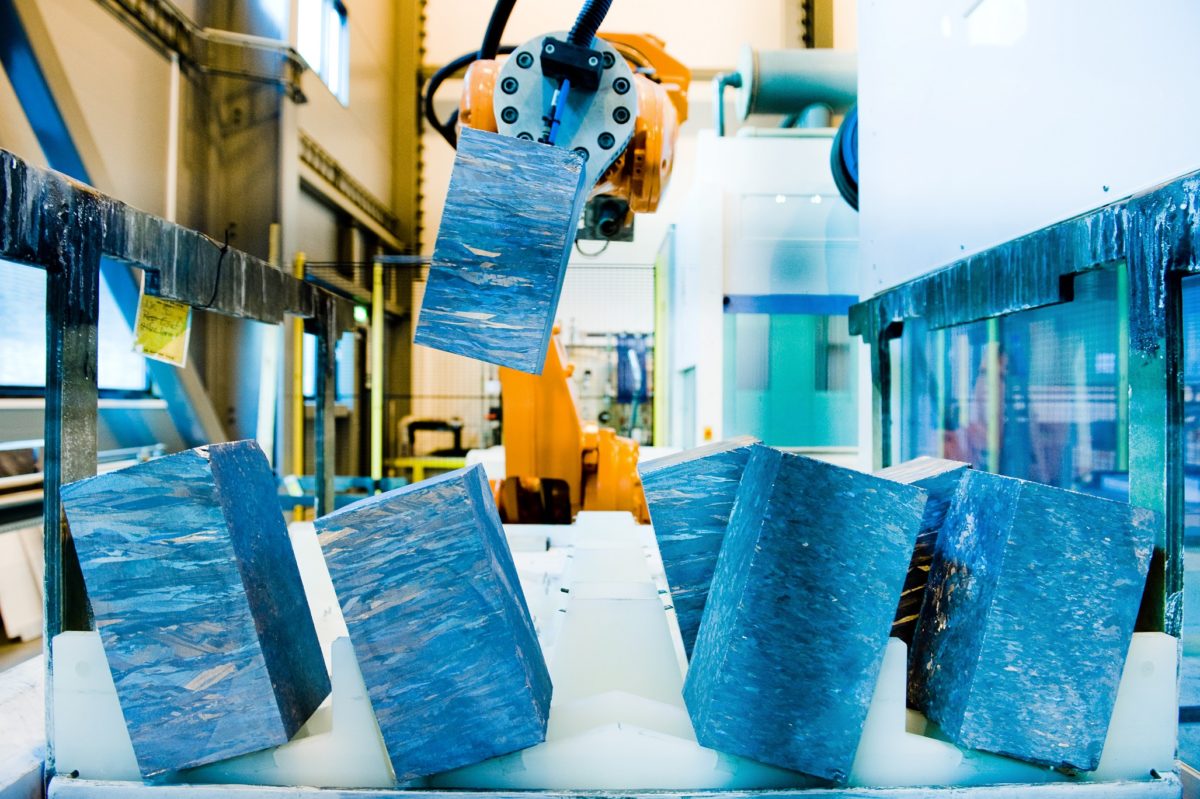
REC Silicon
The module’s structure is warranted for 12 years, with the power production guaranteed at better than a 0.5% annual degradation loss, after an up to 2% loss in the first year – with a projection that after 25 years of production your product will pushing electricity at above 86% of its initially advertised peak output.
The company moved to Singapore in 2008, long before the scaling of the modern solar power industry, in search of stable business and politics, strong shipping prices, and access to highly trained professionals. Wafers, cells, and solar modules are manufactured in the combined facilities (main article image).
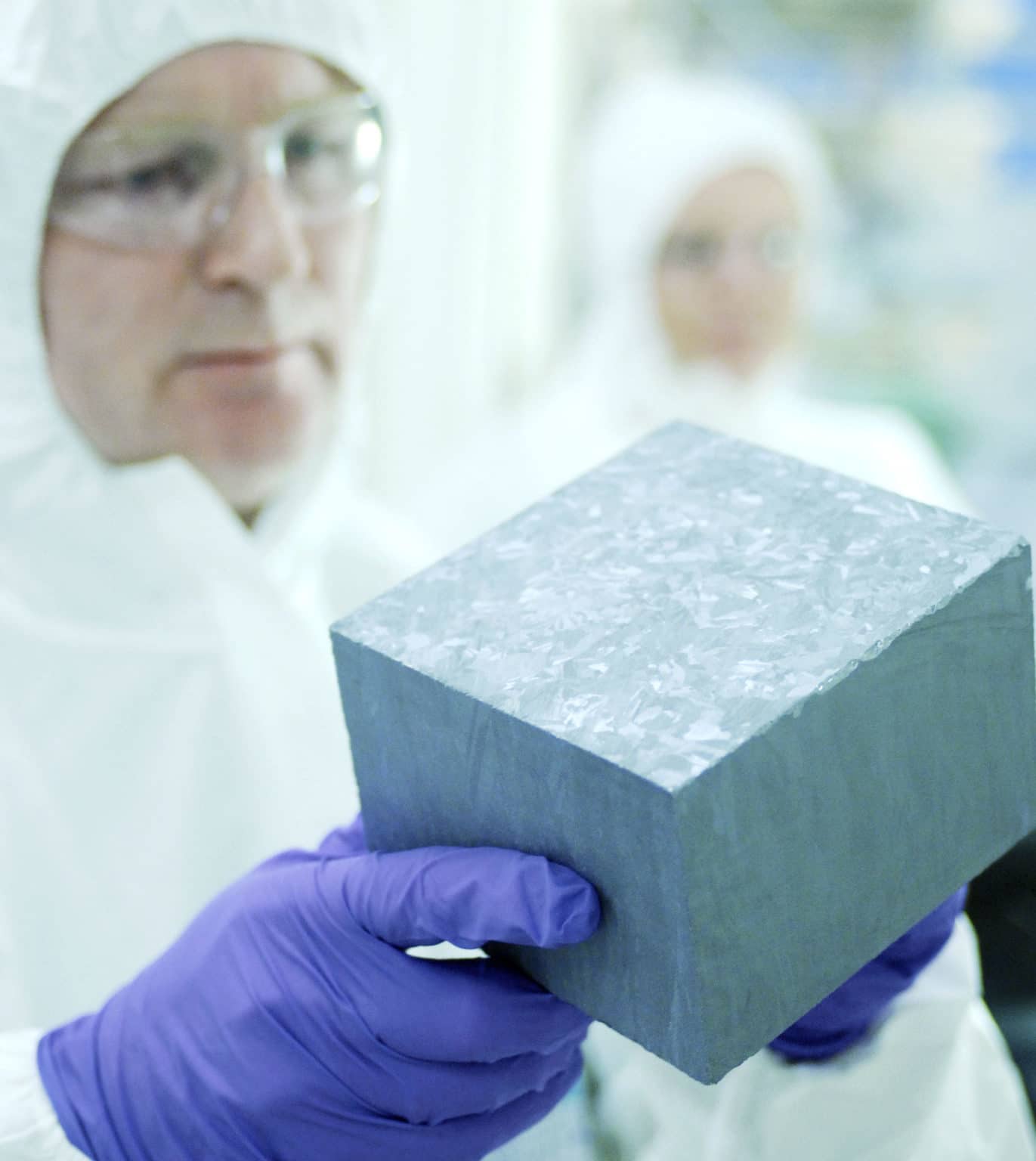
REC
When asked about the costs of getting business done in an expensive market like Singapore, REC noted that because of its highly automated manufacturing process – highly automated since that 2008 move – they have a very low number of personnel on any manufacturing line, and this personnel tilts toward technicians monitoring output versus production personal interacting with product. The final answer was that things like land and salaries, yes – among the most expensive globally in Singapore – are but small components for the company’s all-in costs.
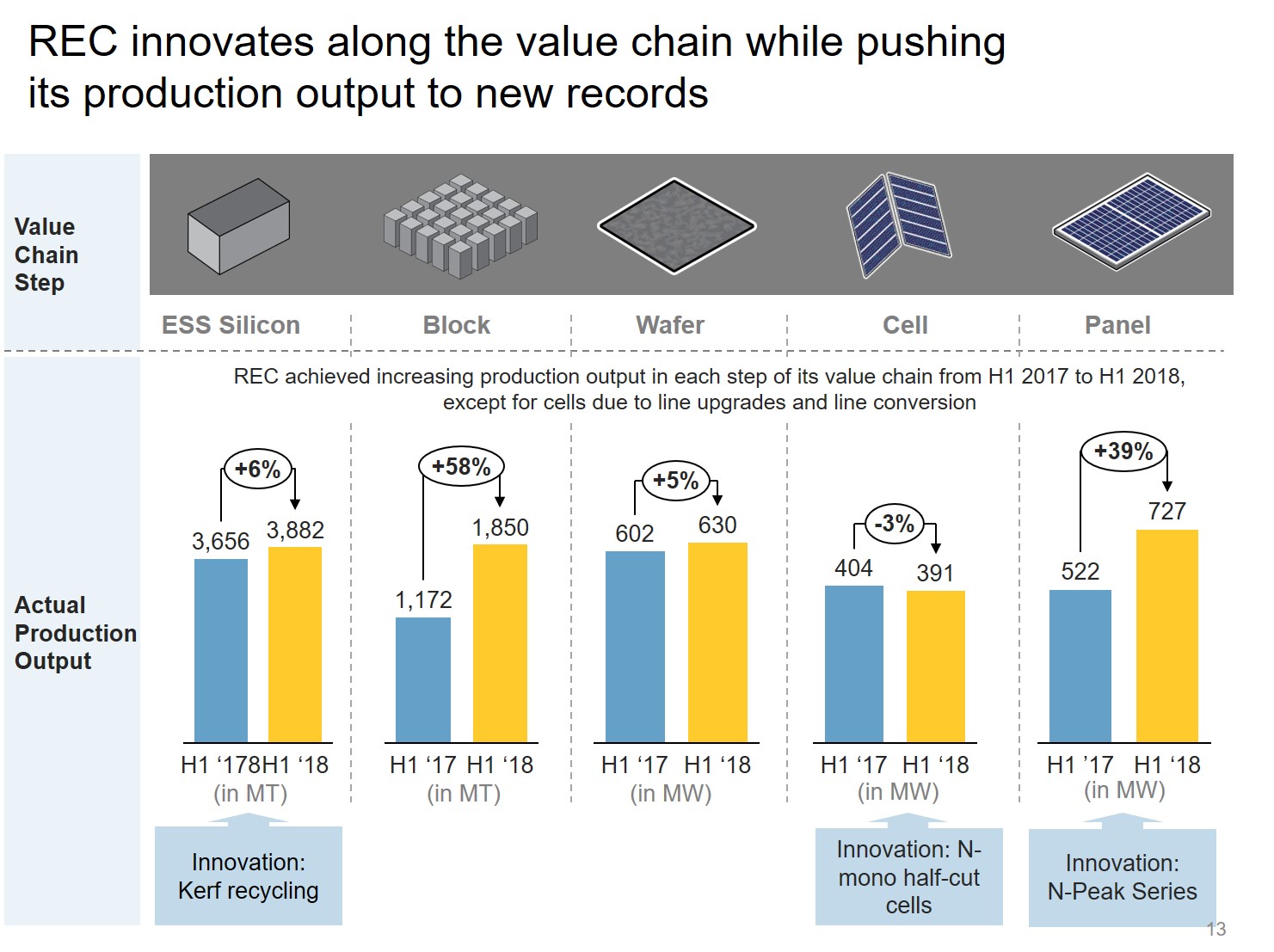
In the end, we’re all just looking for a solar module we can buy, install and stand behind. We want a product that our customers will trust, because most of our project sales are going to come from word of mouth and a solid recommendation. REC hopes you see the value in the peace of mind they’re selling.
This content is protected by copyright and may not be reused. If you want to cooperate with us and would like to reuse some of our content, please contact: editors@pv-magazine.com.
a “sponsored” article?
No money involved from REC/marketing people/etc. I met with them at the conference. I wanted to write about the module so I could show off some new hardware. Turned into me asking questions about why stuff matters. I used to write article on modules a lot at electrek.co – https://electrek.co/guides/solar-panel/, just something I got a chance to do for the first time here.
If anything, pv magazine sponsored my trip to SPI and I feel like I gotta write stuff about the people I met there if I want free room and board again next year. 🙂
Thanks for the link to solar panel electrek
Here all night