This article is the fourth in a series which discusses specific system reliability issues seen in North American systems (click here for the first, second and third articles). Each article focuses on a specific failure mode, giving an overview and examples of defect presentation. A longer summary article diving into a broader industry context and defect prevalence will follow this series.
Most string-level wiring failures result in modules of the string left in a state of open-circuit. This can happen for example if a string fuse is blown or if a connector along the string is missed. However, it is also possible for modules to be wired into a state of short-circuit, which is more of a concern both in terms of long-term module reliability and for site safety. This article discusses the defect mode of short-circuit strings, and the importance of robust site safety protocols.
Strings in open versus short-circuit are simple to distinguish using aerial Infrared inspection, as demonstrated by the example given in Figure 1. When in open-circuit no current is flowing within the string, and each module dissipates its generated power as heat uniformly. Conversely, when in short-circuit, current is flowing and takes the path of least resistance. Inherent variation in cell resistance module to module and within a module results in non-uniform heating, giving a “speckled” look.
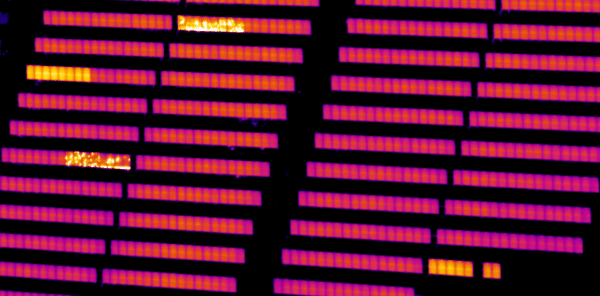
Heliolytics
A string that is wired in short-circuit may be in that state due to being wired in reverse at the combiner. Figure 2 gives an example image of a safety incident that resulted from such an error.
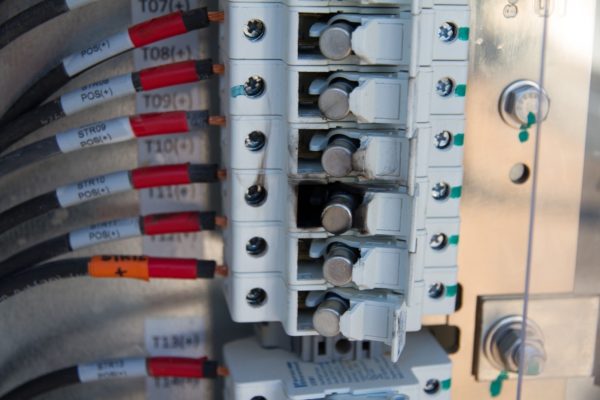
Strata Solar
Another example of how modules can be mis-wired into short-circuit is through module-to-module connection errors. Figure 3 gives an example where the wrong module terminals were connected to each other erroneously within a string when connecting across a tracker structure. This resulted in half of the string wired in open-circuit and half in short-circuit.
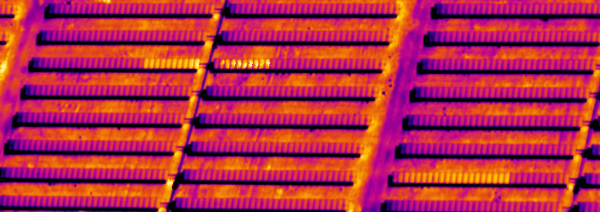
Heliolytics
It is more likely for short-circuit issues to arise during site construction rather than during standard O&M actions. A robust commissioning process, including inspections that will reveal any such occurrences, will both maximize site energy production and more importantly minimize safety risks as early as possible.
To respond to downstream errors that occur between commissioning to day-to-day operations, Strata Solar has implemented a total quality management program that transcends all stages of a project in order to prevent errors that compromise safety. ‘First Time Right’ is Strata’s answer to addressing quality and safety measures properly the first time, thus eliminating the need to treat safety reactively.
“As an EPC and plant operator with over 1.2GW of experience, we have found that aerial infrared images are particularly useful in diagnosing problems in sites with thin film modules where multiple strings are typically wired together using fused harnesses in the field,” says Gabe Cantor, Director of Plant Architecture & New Technology at Strata. “These DC health issues are pernicious and can be hard to diagnose by other means. Defective fuses or connections in these harnesses may not show up in combiner performance monitoring and can even be missed when checking DC voltages and currents in the combiner.”
By adhering to company-wide best practices that put an emphasis on ensuring safety and quality upfront, Strata is focused on preventing short-circuit issues before they start.
This content is protected by copyright and may not be reused. If you want to cooperate with us and would like to reuse some of our content, please contact: editors@pv-magazine.com.
Very Informative. Thanks for taking the time to provide the best information. Enroll for Gate Coaching for more real time information