Polysilicon market analyst Johannes Bernreuter knows the solar polysilicon sector and the global solar supply chain as well as anyone.
In his recent opinion piece, he notes that there is sufficient polysilicon manufacturing capacity outside the Xinjiang region of China to service the U.S. and EU solar markets. The focus on Xinjiang reflects significant sustainability concerns with the industry there – heavy reliance on coal-fired electricity in this energy-intensive sector and the alleged use of forced labor.
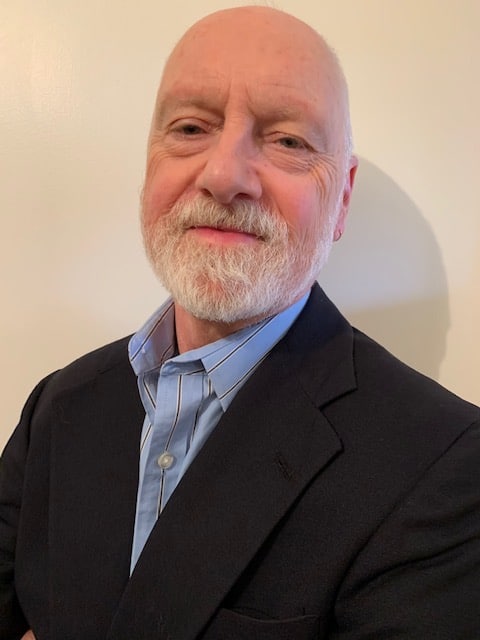
He also argues that a major realignment of the global solar supply chain to entirely avoid Xinjiang polysilicon, which currently represents almost one-half of the world’s total, “will be no cakewalk.”
I agree. But there is more to the story for the global solar industry and solar buyers.
Bernreuter cites my comments to pv magazine USA about the goals of the Ultra Low-Carbon Solar Alliance to decarbonize the solar supply chain and the availability of low-carbon polysilicon in the U.S. and EU. The point I made, which he noted himself, was that this cleaner polysilicon capacity (as well as hydro-powered polysilicon plants in eastern China) was sufficient to provide the U.S. and EU markets with ultra low-carbon solar modules made without Xinjiang polysilicon.
More importantly, I expressed the view that this is merely a first step and if we stop there, we have missed an important opportunity to decarbonize the solar industry.
Solar manufacturing is slated to grow dramatically in the coming decades, to the tune of 10x by 2050 according to DNV GL. If we merely redistribute existing solar production and this growth continues to be concentrated in Xinjiang, carbon pollution associated with solar manufacturing will skyrocket. This would be a deeply ironic prospect for “clean energy.”
A compact industry
Combating climate change and decarbonizing any major industrial sector is indeed no cakewalk, but it is a critical component of achieving a net zero carbon economy. In fact, we have seen global industries like steel, cement and glass take major steps in this direction. Major investors like Blackrock are urging companies to assess their Scope 3 supply chain emissions as part of their carbon reduction goals.
It won’t happen overnight and carbon-sensitive developed economies will surely go first. We believe, however, that by making ultra low-carbon solar a global standard over time, solar buyers and policy makers can send a clear message to the industry that the next major tranche of growth in solar manufacturing must be much cleaner.
Making this transition means locating polysilicon and ingot plants in hydro- and other renewables-rich regions rather than coal-intensive regions. It means higher levels of energy efficiency in those plants. It means a widespread, intentional focus on reducing the carbon footprint of solar manufacturing.
We believe that market demand is a very important element of driving that focus. Companies produce what customers want to buy, and if companies only buy solar modules made with lower carbon footprints, whether directly or in PPAs, that is what the solar industry will produce.
For the solar PV industry and the polysilicon segment in particular, we should stop relying on predominantly coal-fired manufacturing. We must transform the global solar supply chain to become truly sustainable.
Michael Parr is the executive director of the Ultra Low-Carbon Solar Alliance.
The views and opinions expressed in this article are the author’s own, and do not necessarily reflect those held by pv magazine.
This content is protected by copyright and may not be reused. If you want to cooperate with us and would like to reuse some of our content, please contact: editors@pv-magazine.com.
The Ultra Low Carbon Solar Alliance states “Differences in PV supply chain emissions (“embodied” carbon) can have a substantial impact on the greenhouse gas emissions avoided by solar projects. The use of materials with lower embodied carbon in PV panels can reduce the carbon footprint of solar systems by 50 percent, regardless of where the panels are produced.”
The 50% lower carbon footprint claim may be true, but the conclusion does not immediately follow. The IPCC 2014 median estimate for CO2 intensity by electricity source was 48 grams CO2 per kilowatt hour for utility scale solar PV, while the cleanest fossil source was combined cycle gas generation at 490 g/kWh. A solar project that marginally displaces 1 kWh of gas generation prevents emitting 490 – 48 = 442 grams of CO2.
If the solar project is built with “ultra low carbon” components that cut life cycle emissions in half, the emissions averted are instead 490 – 24 = 466 grams of CO2. That’s about 5 percent better. If we’re using the imputed price of carbon emissions to make investment decisions, ultra low carbon solar deployed to reduce fossil combustion can justify perhaps a 5-6% price premium over “regular” solar serving in the same role. If ULCS carries a higher price premium than that, deploying additional “regular” solar megawatts actually abates more CO2 emissions per dollar invested.
The LCA difference between PV and even-better-PV becomes routinely significant only in a world that has already largely decarbonized, and we are sadly still far from that state.