Editor’s note: This article is the fifth in a series which will discuss specific system reliability issues seen in North American systems. Each article will focus on a specific failure mode, giving an overview and examples of defect presentation. A longer summary article diving into a broader industry context and defect prevalence will follow this series.
By Dr. Rob Andrews and Kristine Sinclair, Heliolytics
Bypass diodes are used in silicon PV modules to protect against issues that can arise from local defects. If a cell within a string of cells wired in series is shaded or damaged, it will limit the current production of that string, and can cause a local hot-spot. A bypass diode mitigates this by allowing for an alternative current path. Several bypass diodes are typically used per module, each connected in parallel with a grouping of series connected cells.
Two main failure modes are possible with bypass diodes; failing in open or in short. If a bypass diode fails in open, it can pass no current and it is equivalent to the associated cells not having a bypass diode. This failure mode is insidious – it has no immediately observable effects, but has all the associated safety, reliability, and performance concerns that motivated using bypass diodes in the first place.
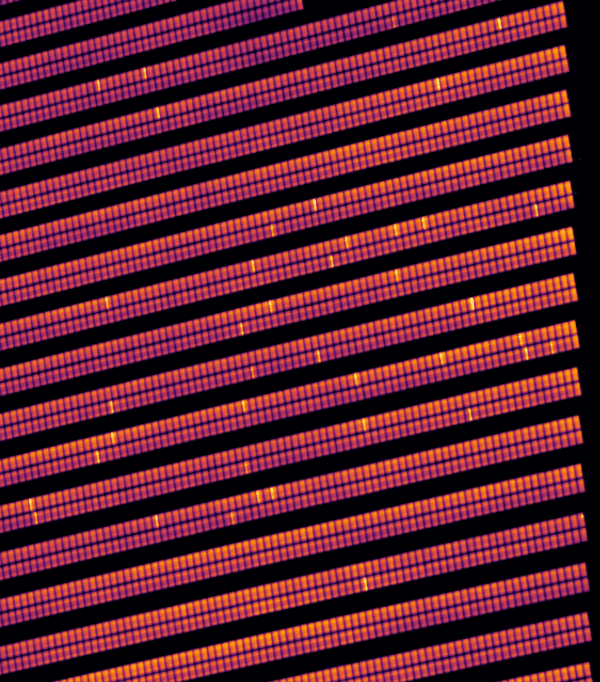
Heliolytics
Conversely, bypass diodes failed in short are simple to observe using IR inspection; the column of cells associated with the shorted diode appears hot (see Figure 1 and Figure 2 for examples). Since the bypass diode now acts as wire conducting electricity, these cells and the power they produce are cut off from site power production. The defected module will also lower power production of other modules within its string by causing a shift off of their maximum power point. Note that this IR anomaly appearance can also have other underlying causes that can be distinguished upon follow-up ground investigations, such as faulty solder joints in the junction box or module string interconnect tabbing ribbon.
Bypass diodes failed in short are a common defect mode that Heliolytics observes, often leading to module warranty claims. Clustering of defected modules may be observed across a site, indicating correlation with module manufacturing batch. When this issue appears on newly constructed sites, it indicates an infant mortality failure mode. Post commissioning, a regular O&M schedule with the ability to detect this issue early on in module life is critical. If a serial defect is suspected, full site surveys to assess defect scope on an on-going basis, coupled with ground-based sampled investigations, proves an effective approach to a warranty claim.
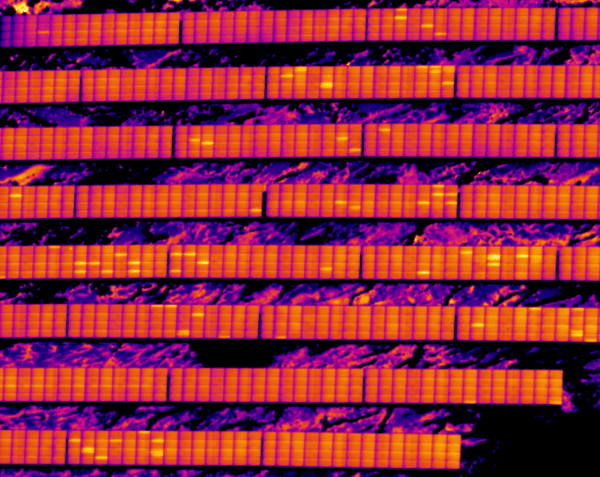
Heliolytics
The prevalence of this serial defect points to a systematic and therefore solvable issue in the industry. Investors and owners can de-risk their asset before installation by requiring module manufacturer factory audits and accelerated life testing by manufacturing batch. Bypass diodes will be purchased for integration by the module manufacturer, and insufficient quality procedures on their part may cause faulty parts to be built into product.
“The best thing to do is stop the problem before it happens,” notes Jon Previtali, the director of technology for a major bank providing tax equity finance for PV systems. “It’s good to ensure module makers are checking bypass diodes electrically, not just visually before they install them.”
“You can do that through factory audits. If a diode latent defect creeps into the module, it can often be seen through typical damp heat test done as part of the IEC 61215 standard, but only if you have a third-party lab actually do the test on a sample of the modules you’re getting. Bypass diode failures sometimes cause the junction box to deform due to heat, but they also clearly cause hot spots under infrared when the modules are energized.”
“You can see that after the damp heat test or in the field. Safety is the primary concern if an issue like this pops up. If you’re super confident the issue isn’t so bad it will cause a fire and you can’t simply replace the modules, try to get a serial defect warranty clause added to module warranty agreement. That way if the diodes start to cause lower than warranted power production, you can make a warranty claim on the whole batch after a statistically significant number fail, not each one. Infrared thermography from the air is a great way to get data for a warranty claim, no doubt. It works.”
This content is protected by copyright and may not be reused. If you want to cooperate with us and would like to reuse some of our content, please contact: editors@pv-magazine.com.
By submitting this form you agree to pv magazine using your data for the purposes of publishing your comment.
Your personal data will only be disclosed or otherwise transmitted to third parties for the purposes of spam filtering or if this is necessary for technical maintenance of the website. Any other transfer to third parties will not take place unless this is justified on the basis of applicable data protection regulations or if pv magazine is legally obliged to do so.
You may revoke this consent at any time with effect for the future, in which case your personal data will be deleted immediately. Otherwise, your data will be deleted if pv magazine has processed your request or the purpose of data storage is fulfilled.
Further information on data privacy can be found in our Data Protection Policy.